引言
隨著表面工程的發(fā)展,涂層技術(shù)得到了廣泛應(yīng)用。有機涂層存在復(fù)雜服役環(huán)境下力學(xué)強度低、不耐磨
、易脫落、壽命短等問題,其可靠性無法得到有效保障[1-2]。金屬涂層以出色的力學(xué)性能與耐久性脫
穎而出,有望增強材料性能,延長服役壽命,具有良好的應(yīng)用潛力,研發(fā)高性能金屬涂層材料已成為工程領(lǐng)
域的迫切需求[3-5]。
鈦及鈦合金因良好的低溫性能與優(yōu)異的耐蝕性、低密度、高強度等特性,廣泛應(yīng)用在海洋工程、航空航
天、生物醫(yī)療等諸多領(lǐng)域,被譽為“21世紀的金屬”[6]。盡管鈦具有諸多優(yōu)點,但高活性、易氧化
、制備加工成本高、后續(xù)加工困難等問題也限制了其推廣應(yīng)用。為了降低工程應(yīng)用成本,工業(yè)生產(chǎn)中常采
用在低成本金屬表面沉積貴金屬層的手段,使低成本金屬承擔(dān)復(fù)雜力學(xué)載荷,由表層貴金屬來滿足特定表面
性能[7]。覆有鈦涂層的“復(fù)合型材料”可充分發(fā)揮涂層與基體各自的優(yōu)勢,規(guī)避各自缺點,獲得單一
金屬無法達到的綜合性能[8]。
由于鈦材熔點高且易氧化,現(xiàn)常用噴涂、激光熔覆、氣相沉積等方法在同/異種基體表面制備厚度均
勻的鈦涂層。通過對涂層元素、成分的調(diào)整和結(jié)構(gòu)設(shè)計可制得面向不同服役環(huán)境應(yīng)用的鈦涂層,并根據(jù)涂層特性進行后處理,以進一步改善涂層性能,減少孔隙、裂紋等缺陷對
材料的不良影響[9-10]。本文將對鈦涂層常用制備技術(shù)與后處理手段進行介紹,并結(jié)合國內(nèi)外研究報
道對鈦涂層在海洋工程、生物醫(yī)療、航空航天與能源化工等領(lǐng)域的應(yīng)用研究進展進行闡述,以期為相關(guān)行業(yè)
人員提供參考。
1、鈦涂層材料常用制備技術(shù)
涂層能顯著增強材料表面性能,使基體表面功能化[11]。在材料表面制備鈦涂層,不僅可利用鈦材
的優(yōu)異性能,亦可顯著降低材料成本、縮短制備周期,具有顯著的應(yīng)用優(yōu)勢。
涂層制備是至關(guān)重要的一步,根據(jù)不同成分特性與應(yīng)用需求的鈦涂層選擇合適的制備工藝將有助于材料
性能的提升,目前常用的鈦涂層制備技術(shù)主要有等離子噴涂與超音速火焰
噴涂等傳統(tǒng)熱噴涂技術(shù),以及冷噴涂、激光熔覆和氣相沉積等技術(shù)[5,12-15]。
1.1熱噴涂
熱噴涂是用火焰、等離子射流、電弧等作為熱源將涂層材料(絲、棒、粉)加熱到熔融或半熔融狀態(tài),
并高速噴射至基體表面使之凝固沉積形成涂層的技術(shù)[4]。熱噴涂具有靈活性與通用性的特點,根據(jù)噴
涂顆粒速度、顆粒溫度和平均原料尺寸特征,可對典型噴涂技術(shù)進行分類,如圖1所示[16]。
等離子噴涂、超音速火焰噴涂、電弧噴涂等傳統(tǒng)熱噴涂技術(shù)在鈦涂層制備領(lǐng)域有著廣泛應(yīng)用[12-13
,17],由圖1可知該類技術(shù)普遍都需通過高溫將原料鈦粉加熱熔融用以噴涂。而鈦化學(xué)性質(zhì)十分活
潑,在高溫下極易與空氣中氧、氮等氣體發(fā)生反應(yīng),使得涂層中化合物含量與孔隙率普遍較
高,如Ishikawa等[18]采用火焰噴涂在碳鋼表面制備了鈦涂層,由于噴涂過程中涂層材料未被
充分保護,涂層中將近一半的鈦轉(zhuǎn)化為金屬化合物,使得涂層孔隙率過高。研究表明,噴涂氣氛環(huán)境對涂
層質(zhì)量有著重要影響,保護氣氛或真空環(huán)境可降低鈦的氧化程度,有利于獲得低氧、高致密的鈦涂層[14
]。
在傳統(tǒng)熱噴涂技術(shù)中,涂層材料會經(jīng)歷熔化與快速凝固的變化過程,氧化物與孔隙難以避免,同時高溫
下涂層材料會發(fā)生相變,影響涂層性能[4,19]。鑒于傳統(tǒng)熱噴涂涂層的高孔隙率特征,熱噴涂類技
術(shù)不適用于制備高耐蝕性防護涂層,例如,曲彥平等[13]研究發(fā)現(xiàn)電弧噴涂制備的鈦涂層因高孔隙率需
后續(xù)封孔處理才能獲得耐蝕性。而在骨植入物的多孔涂層制備方面,熱噴涂類技術(shù)具有一定優(yōu)勢,例如,
大氣等離子體噴涂制備的多孔TiO2涂層可改善植入物的蛋白質(zhì)吸附與骨整合能力[20]。綜上所
述,熱噴涂技術(shù)在制備熔點高、塑性差的鈦化合物涂層方面更有優(yōu)勢[21];而鈦及其合金塑性較好,易
發(fā)生高溫氧化,故制備鈦金屬或鈦合金涂層可采用噴涂溫度較低的冷噴涂技術(shù)[22]。
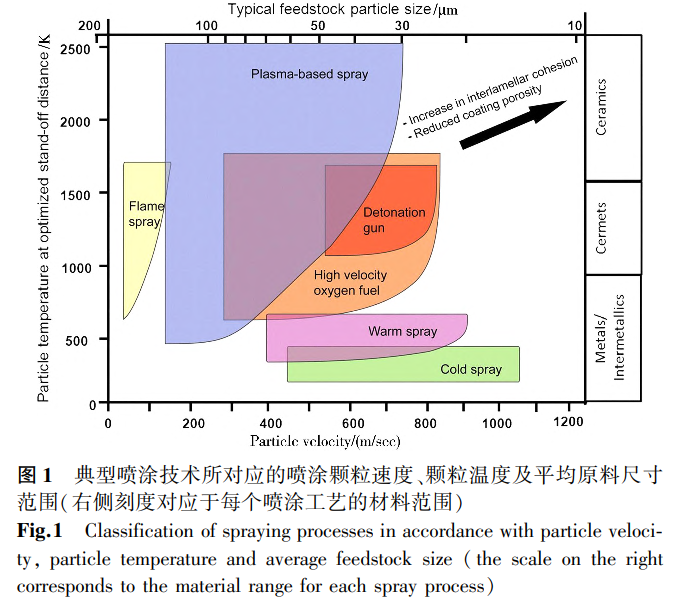
1.2冷噴涂
冷噴涂是利用電能將高壓氣體(He、N2等)加熱到一定溫度,并在拉瓦爾管加速作用下使粉末顆
粒高速沉積至基體表面形成涂層的技術(shù)[3]。冷噴涂過程中顆粒未熔化,其是以固體形式進行沉積,由
于先沉積顆粒持續(xù)受到后沉積顆粒的撞擊,涂層愈加致密,與基體結(jié)合更加牢固,因此冷噴涂涂層通常具有
低的孔隙率、高的沉積效率與結(jié)合強度[23-24]。與傳統(tǒng)熱噴涂相比,冷噴涂最大優(yōu)勢在于低溫固態(tài)
沉積,低的噴涂溫度避免了鈦的氧化以及高溫對基體的不良熱影響[22],如Gardon等[25]
為防止聚合物基底的熱分解,采用冷噴涂在聚醚醚酮(PEEK)表面制得了厚度均勻、結(jié)合良好的鈦涂
層。
對冷噴涂而言,噴涂顆粒需達到一定的臨界速度才能沉積形成涂層,推進氣體種類、噴涂溫度與噴涂壓
力等因素對涂層質(zhì)量有著顯著影響[24]。He具有高載氣速度特性,以其為推進氣體可獲得高的顆粒
速度,有利于增加顆粒變形量、促進顆粒扁平化,從而獲得更為致密的鈦涂層[26],但He成本高昂
,實際生產(chǎn)中多采用He、N2混合氣[27]。Gulizia等[23]指出,提高噴涂溫度與壓
力也有助于提升冷噴涂涂層致密度,且溫度影響更為顯著,但溫度過高時,涂層中O與N含量增大,導(dǎo)
致鈦涂層性能下降。除上述影響因素外,西安交通大學(xué)李長久教授團隊[22]綜述了冷噴涂粉末形態(tài)、
基體狀態(tài)與噴嘴形狀等因素對鈦涂層性能的影響,為冷噴涂鈦涂層的研究和應(yīng)用提供了一定的理論參考。
冷噴涂沉積形成的鈦涂層具有硬度高、塑性差的特點,且涂層內(nèi)部常存在因顆粒結(jié)合不良而產(chǎn)生的孔隙
等缺陷。
為了改善冷噴涂金屬涂層的性能,西北工業(yè)大學(xué)李文亞教授[28]提出“冷噴涂+”概念,即將冷噴
涂與特定工藝(如噴丸、熱軋、熱處理等)相結(jié)合,以減小涂層孔隙率、改善涂層結(jié)合強度與強塑性,該研
究為促進冷噴鈦涂層的工業(yè)化應(yīng)用提供了技術(shù)指導(dǎo)。結(jié)合上述對鈦涂層噴涂制備技術(shù)的闡述,現(xiàn)將鈦涂層
常用噴涂制備技術(shù)的優(yōu)缺點總結(jié)于表1[14,16,29-30]。
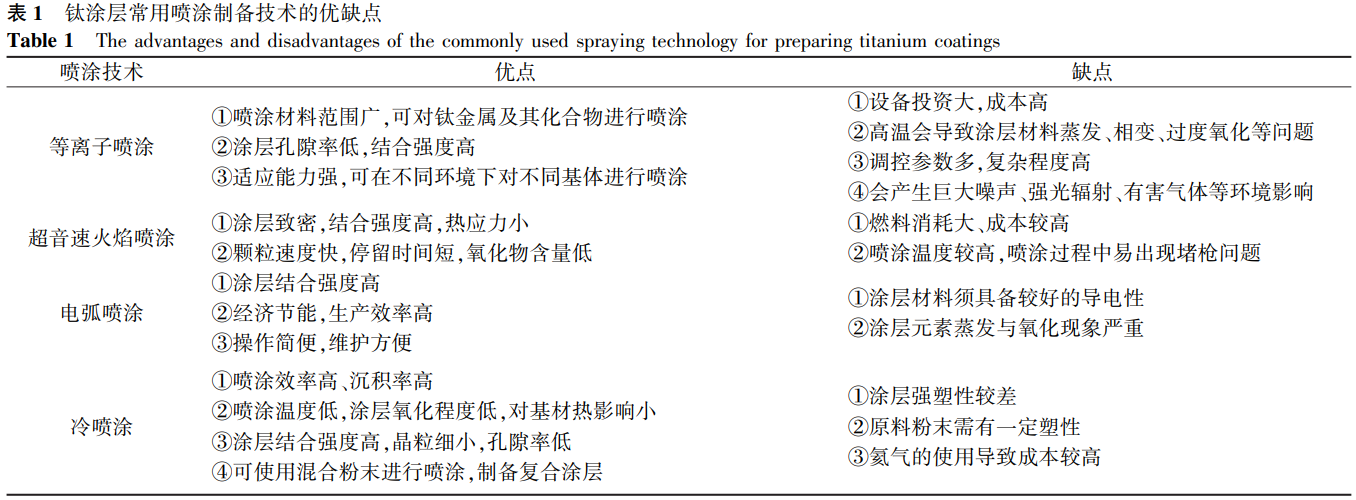
1.3激光熔覆
激光熔覆是粉體經(jīng)高能激光束輻照后與基體表面熔合并快速凝固形成涂層的工藝方法[31]。激光
熔覆與噴涂有顯著的不同,由于激光熔覆的高溫特性,涂層中孔隙可大量消失,從而使組織更加均勻,涂層內(nèi)部與結(jié)合界面處原子通過相互擴散可形成良好的冶金結(jié)合,同時熔覆
后的快冷“淬火”作用使得涂層具有高硬度,故激光熔覆鈦涂層在耐磨、耐蝕與高溫抗氧化領(lǐng)域有著廣泛應(yīng)
用[5]。
采用激光熔覆制備鈦涂層時,需考慮Ti涂層與基體之間的相容性問題,一般為了保障熔覆層具有良
好的力學(xué)性能,需使涂層成分盡可能接近基體金屬,保證涂層與基體金屬之間良好熔合[5]。Wang等[32]在TC4表面采用激光熔覆制得與基體冶金結(jié)合良好的
純鈦涂層,熔覆形成的鈦涂層在細晶強化、晶界強化和第二相強化的共同作用下顯著提升了TC4的耐磨
性與高溫服役性能。但若Ti涂層與基體之間相容性差,則很難獲得高質(zhì)量涂層,如西北有色院王培等
[33]采用激光熔覆技術(shù)在Q235鋼表面制備鈦涂層,冷卻后出現(xiàn)熔覆Ti層表面不平整的冶金不
相容現(xiàn)象。其原因在于Ti與Fe之間熱物理性質(zhì)(導(dǎo)熱率、膨脹系數(shù)等)差異較大,且Ti與F
e基本不互溶,熔覆后界面存在大量的TixFey脆性金屬化合物,導(dǎo)致Fe基體與Ti涂層間
結(jié)合不牢固[34]。針對該問題,通過添加與Fe和Ti均有良好相容性的Ni中間層,提高了
涂層結(jié)合強度,改善了熔覆層質(zhì)量[33]。北京科技大學(xué)王志煒[35]在激光熔覆制備Q235鋼
基體表面鈦/釩涂層的研究中添加了釩中間層,顯著提升了鈦涂層與異種基體之間的結(jié)合質(zhì)量,涂層結(jié)合
強度高達285MPa。除上述提到的基體與涂層間相容性問題外,激光熔覆技術(shù)因較高的冷卻速率導(dǎo)
致硬質(zhì)鈦涂層易出現(xiàn)變形、開裂與元素成分偏析等,有待進一步研究改進[5,36]。
1.4氣相沉積
氣相沉積是在真空中將涂層原料蒸發(fā)成原子、分子或離子然后沉積至基體表面形成功能性薄膜的技術(shù),
按照原理可分為物理氣相沉積(PVD)與化學(xué)氣相沉積(CVD)兩大類[29]。PVD對基
體熱影響小,為低溫沉積技術(shù),同時PVD可實現(xiàn)對涂層成分及結(jié)構(gòu)的調(diào)控,Xiao等[37]采用
PVD技術(shù)在Ti(C,N)金屬陶瓷基體上沉積了TiAlN涂層,研究發(fā)現(xiàn)降低基體晶粒尺寸可提
升涂層的成核率與致密度。相較于PVD技術(shù),CVD可實現(xiàn)在復(fù)雜形狀基材上的膜層制備,并且由于
其原料(前驅(qū)體)為化合物,涂層制備時不易出現(xiàn)Ti氧化問題[38]。Guo等[15]以Ti-
TiCl4體系反應(yīng)合成的TiCl2為前驅(qū)體,采用CVD在316L不銹鋼基體上制得了致密
且與基體結(jié)合良好的Ti涂層。Jin等[39]對CVD制備鈦涂層的相關(guān)研究進行了綜述,為新
型鈦涂層的開發(fā)提供了參考。CVD工藝無需真空環(huán)境,避免了昂貴真空設(shè)備的使用,但制備時可能產(chǎn)生
有毒氣體,同時過高的沉積溫度對涂層質(zhì)量也會產(chǎn)生影響[38,40]。
總之,氣相沉積可實現(xiàn)高熔點、難熔鈦金屬化合物的沉積成膜,多用于硬質(zhì)耐磨涂層的制備,如在刃具
、模具、耐磨零件上沉積各種鈦的碳化物、氮化物、硼化物等超硬膜[39]。
但由于制備成本高、沉積速率低等,該技術(shù)的大規(guī)模應(yīng)用在一定程度上受到限制[38,40]。最后
,結(jié)合本節(jié)對鈦涂層常用制備方法的闡述,將各類技術(shù)的特征總結(jié)、對比于表2[5]。
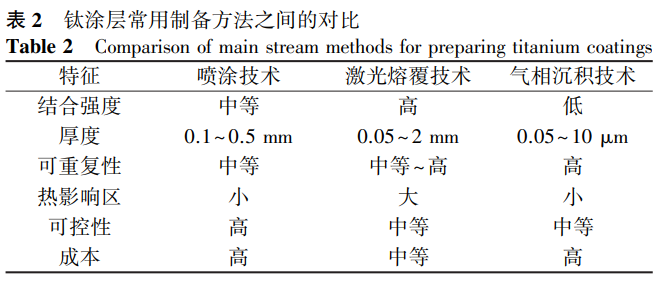
2、鈦涂層的后處理技術(shù)
由于制備手段的局限,鈦涂層很難達到如熔鑄金屬那樣接近100%的致密度。涂層中通常會留有孔
隙、裂紋等缺陷,對涂層進行適當(dāng)后處理可減少涂層缺陷,改善涂層質(zhì)量。目前常用的后處理方法包括封
孔、噴丸、熱軋與熱處理等[41-45]。
2.1封孔處理
缺陷的存在會降低涂層的力學(xué)性能、削弱其對基體的保護效果,當(dāng)缺陷涂層暴露于腐蝕環(huán)境中時,腐蝕
介質(zhì)會通過缺陷到達基體表面并發(fā)生腐蝕反應(yīng),腐蝕產(chǎn)物在界面積累,致使涂層龜裂、脫落甚至失效,喪失對基體的保護作用[41,44,46]。
封孔處理主要是利用刷涂、浸漬等手段使封孔劑滲入至涂層內(nèi)部,達到填充孔隙、改善涂層性能的效果
。為更好地提升封孔效果,一般常選用粘度低、滲透性好且具有良好力學(xué)性能的有機材料作為封孔劑[4
6]。Ishikawa等[18]通過實驗證明了樹脂封孔后的鈦涂層具有優(yōu)異的耐氯化物腐蝕能力
。shi等[47]以環(huán)氧樹脂為封孔劑對大氣等離子噴涂制備的鎳鈦涂層進行表面封孔處理,空蝕實驗
表明封孔處理增強了涂層內(nèi)片層間的結(jié)合力,提高了鎳鈦涂層抑制裂紋擴展與抗空蝕的能力[48]。M
orończyk等[49]采用環(huán)氧樹脂對AZ91E鎂合金基體上的鈦涂層進行封孔處理,并使用
3.5%NaCl溶液浸泡實驗考察涂層的耐蝕性,發(fā)現(xiàn)未封孔的涂層中存在互連孔隙,因而腐蝕介質(zhì)能
夠快速滲透到基材表面,在界面處發(fā)生電偶腐蝕,涂層在浸泡24h后脫落,而經(jīng)封孔后的涂層具有良
好的耐蝕性,可實現(xiàn)對基材長達1000h的保護。封孔處理除提升涂層耐蝕性外,還可賦予涂層功
能性,Bi等[50]采用低表面能的聚二甲基硅氧烷(PDMS)對等離子噴涂的金屬陶瓷復(fù)合涂層進
行封孔處理,如圖2所示,提升了涂層的防污能力,為防污鈦涂層的設(shè)計提供了參考。
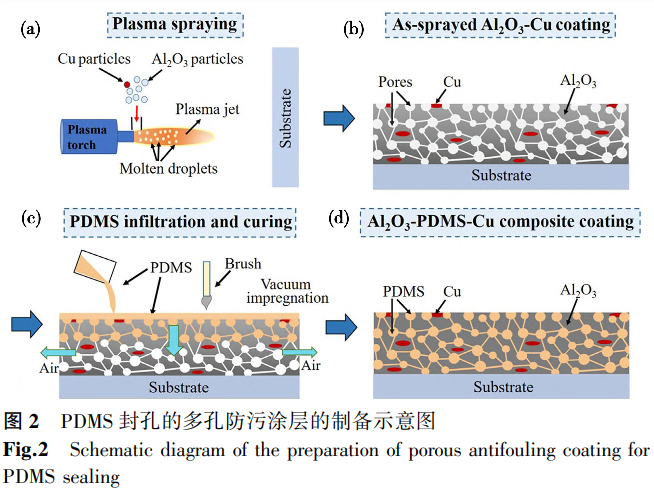
2.2噴丸處理
噴丸處理可使材料表面發(fā)生塑性變形,產(chǎn)生殘余壓應(yīng)力與應(yīng)變層,并且可提升工件抵抗拉應(yīng)力的能力,
抑制工件內(nèi)部微裂紋擴展,使其疲勞壽命、抗應(yīng)力腐蝕能力顯著提高[51]。
對鈦及其合金涂層而言,在噴丸的夯實作用下,孔隙率可得到大幅降低,從而提升致密度與耐蝕性能[
52]。根據(jù)噴丸與鈦涂層沉積的先后順序,可將噴丸處理分為前噴丸、原位噴丸與后噴丸[3]三類。
其中前噴丸與后噴丸處理對多種技術(shù)制備的鈦涂層均可適用[53-54];原位噴丸是結(jié)合冷噴涂特點而提
出的[42],該工藝向原料粉末中摻入尺寸較大的噴丸顆粒,噴涂時由于噴丸顆粒未達到沉積的臨界速度
,故在到達表面時發(fā)生反彈,利用其反彈前的撞擊力輔助顆粒變形,從而起到原位鍛造的效果,其示意圖如
圖3所示[55]。西安交通大學(xué)李長久教授團隊[42,55]研究發(fā)現(xiàn),在冷噴涂-原位噴丸技術(shù)中
,噴丸顆粒的摻入比例、噴丸種類、噴涂溫度等因素對涂層質(zhì)量皆會產(chǎn)生影響。
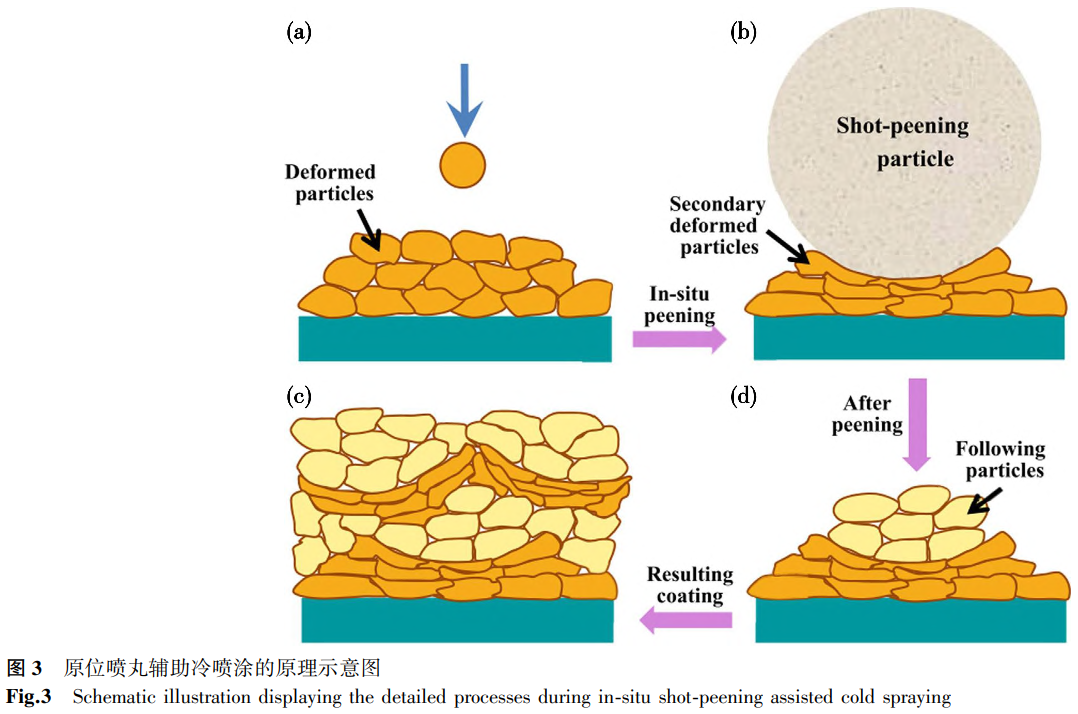
2.3熱軋?zhí)幚?/p>
熱軋?zhí)幚砜稍跓?力耦合作用下降低鈦涂層內(nèi)部缺陷,改善涂層內(nèi)部顆粒界面結(jié)合,提高涂層致密度與內(nèi)
聚強度,提升涂層力學(xué)性能[56]。與噴丸處理類似,由于熱軋?zhí)幚硪彩窃谕饬ψ饔孟率共牧习l(fā)生塑性
變形,故該工藝不適用于硬度大、塑性差的鈦金屬化合物涂層的后處理。Li等[57]通過對304
不銹鋼基底表面的冷噴純Ti涂層進行熱軋,制得了強界面結(jié)合的全致密Ti/304不銹鋼復(fù)合
結(jié)構(gòu)材料,其在3.5%NaCl溶液中表現(xiàn)出與純Ti相當(dāng)?shù)哪臀g性。中國科學(xué)院金屬所熊天英教
授團隊采用冷噴涂-熱軋工藝(工藝流程如圖4所示)制得了鈦/鋼層狀復(fù)合材料,系統(tǒng)研究了軋制溫度、
下壓量等參數(shù)對鈦/鋼層狀復(fù)合材料性能的影響[43,58-59],在最佳工藝參數(shù)下制得的鈦/鋼層
狀復(fù)合材料的拉伸強度、延伸率和界面剪切強度分別可達599MPa、36%和309MPa,遠高于GB/T 8547-2019中的規(guī)定,同時具有良好的可加工性與耐蝕性,整體性能優(yōu)于傳統(tǒng)軋制法
與爆炸法制得的鈦/鋼復(fù)合材料[56]。
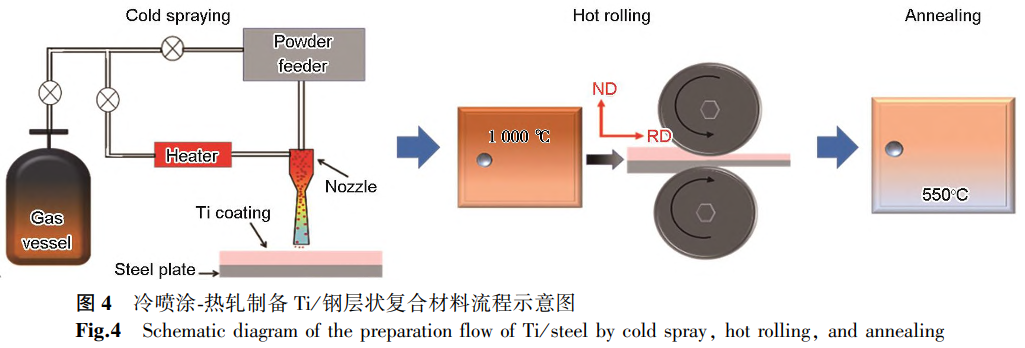
2.4熱處理
熱處理可通過調(diào)控鈦涂層微觀組織達到提高涂層結(jié)合強度、增強涂層韌性與釋放殘余應(yīng)力的效果,是涂
層后處理方式中較為簡單且易實現(xiàn)工程應(yīng)用的手段[22]。為提升涂層性能,Molak等[45]對覆有鈦涂層的鋁合金試樣進行退火熱處理,經(jīng)回復(fù)、再結(jié)晶和晶粒長
大過程,涂層孔隙合并,孔隙體積與數(shù)量顯著減少,且沉積顆粒之間的大部分界面消失,冶金結(jié)合面積增
加,從而使涂層性能得以提升。陳建強等[17]研究發(fā)現(xiàn),對火焰噴涂制備的鈦涂層進行850℃×
4h的熱處理可使涂層的孔隙率降至1.8%,結(jié)合強度增至50MPa,同時自腐蝕電流降低約1
3%。從上述研究可見,熱處理使涂層孔隙減小,涂層質(zhì)量提升,但Li等[44]研究發(fā)現(xiàn)當(dāng)涂層內(nèi)
部孔隙尺
寸過大時,熱處理對鈦涂層性能改善并不明顯。激光熔覆鈦涂層內(nèi)部會存在較大的殘余拉應(yīng)力,在外
力誘導(dǎo)下易出現(xiàn)應(yīng)力集中和微裂紋,翟永杰等[60]通過在500℃下對激光熔覆Ti2SC/T
iS涂層進行真空熱處理,有效緩解了殘余拉應(yīng)力的作用,改善了涂層的摩擦學(xué)性能。在生物醫(yī)用材料領(lǐng)
域,對抗菌涂層進行熱處理還可實現(xiàn)抗菌離子的受控釋放,提高涂層的抗菌性能[61]。
3、鈦涂層應(yīng)用研究進展
隨著科技進步與工業(yè)發(fā)展,近年來各行各業(yè)對性能優(yōu)異的功能性涂層需求愈加迫切,鈦及鈦合金因高比
強度、極佳的耐腐蝕性等諸多卓越特性脫穎而出,功能性鈦涂層的研發(fā)在海洋工程、生物醫(yī)療、航空航天等
領(lǐng)域備受關(guān)注[3,5,12,14]。
3.1海洋工程領(lǐng)域
海洋蘊含豐富資源,具有巨大的開發(fā)價值,但金屬材料在復(fù)雜的海洋環(huán)境中會遭受腐蝕與生物污損,服
役壽命大幅縮短,對國民經(jīng)濟造成巨大損失[62]。鈦涂層具有較高的力學(xué)強度、極佳的耐蝕性,可延
長海洋環(huán)境中金屬的服役壽命,降低工程成本,為海洋工件長久、高效的工程化運作提供重要支持[12,
63]。
鋼材因高強度、低成本等而在海洋工程中應(yīng)用廣泛[64-65],但鋼材耐蝕性普
遍較差,通過在其表面沉積鈦涂層可顯著提升鋼材的耐蝕性,延長服役壽命。深海中材料服役環(huán)境惡劣,
而傳統(tǒng)有機防腐涂層耐久性差,Li等[63]為提高X80管線鋼在深海環(huán)境下的耐蝕性能,在其表
面制備了孔隙率為0.93%的冷噴鈦涂層,該涂層在40MPa靜水壓力的模擬深海環(huán)境中致鈍電流
密度可保持在10-7A·cm-2量級,有效保護了基體。不銹鋼耐蝕性較傳統(tǒng)鋼材雖有所改善,但
在富Cl-的海水環(huán)境中仍會出現(xiàn)嚴重的點蝕,王治中等[66]采用冷噴涂在304不銹鋼表面制備
了自腐蝕電流密度遠低于基體的TC4涂層,有望大幅降低不銹鋼在海洋環(huán)境中的點蝕風(fēng)
險。目前鈦/鋼復(fù)合板已在海洋構(gòu)筑物建造、船舶等領(lǐng)域?qū)崿F(xiàn)了工程應(yīng)用,如日本跨海大橋的橋柱[
64]等,但暴露在海水中的鈦/鋼復(fù)合板端面會出現(xiàn)電偶腐蝕。為了減輕電偶腐蝕帶來的危害,伍廉
奎等[65]在鈦/鋼復(fù)合板端面沉積了孔隙率為1.14%的冷噴鈦涂層,經(jīng)測試,該涂層表現(xiàn)出高
極化阻抗(70.07kΩ·cm2)與良好的耐鹽霧腐蝕能力,有效阻止了侵蝕性離子滲透,從而顯著
提升了鈦/鋼復(fù)合板在海洋環(huán)境中的服役性能。在工程實踐方面,湖北超卓航科公司采用冷噴涂制得的耐
蝕海洋鈦銅管道(如圖5a所示)已在航海領(lǐng)域得到工程化應(yīng)用;南京中遠海運船舶設(shè)備配件有限公司提
出的冷噴涂制備鈦合金涂層以提高船舶管路系統(tǒng)耐蝕性的方法具有巨大的應(yīng)用潛力[67]。
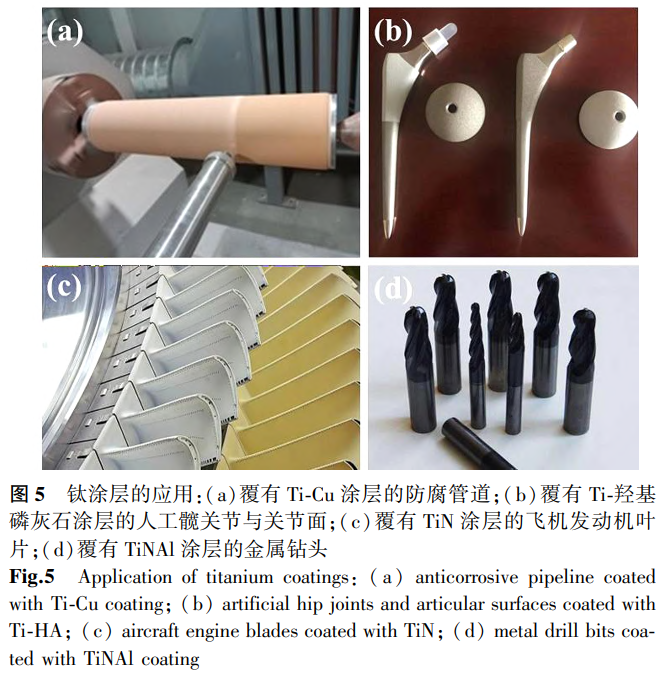
鈦材因優(yōu)異的耐蝕性,在船體結(jié)構(gòu)件、潛艇耐壓殼體、管道等海洋工程材料中得到廣泛應(yīng)用[68]。
但鈦由于生物相容性差,在海洋環(huán)境中會面臨嚴峻的生物污損問題[69]。附著在材料表面的大量污損物會增加船舶行駛阻力,降低探測器靈敏度,對船舶、海上公共設(shè)施、
水產(chǎn)養(yǎng)殖等造成一系列嚴重危害[70],如何在保有鈦涂層良好耐蝕性的基礎(chǔ)上賦予其防污性能是當(dāng)前有
待攻克的關(guān)鍵課題。通過分析海洋污損生物形成過程,可確定生物污損防治的核心點在于抑制調(diào)節(jié)膜或細
菌生物膜的形成或粘附[62]。目前防污鈦涂層的設(shè)計思路大致分為兩大類,一是向涂層中加入Cu[
12]、Ag[71]、Zn[72]等毒性元素,通過釋放毒性離子毒殺粘附在材料表面的生物膜與細
菌等來提高涂層防污性。例如,鄭州大學(xué)田佳佳團隊[12]采用等離子噴涂制得了Cu/Ti交替
復(fù)合涂層,得益于電偶腐蝕促Cu2+釋放與涂層自拋光防污損生物粘附[73]的綜合作用,該涂層具
有接近100%的抑菌率,實現(xiàn)了高效防污,同時防污壽命為傳統(tǒng)有機涂層的兩倍,其防污機理如圖6
所示。二是對涂層進行表面改性或仿生結(jié)構(gòu)設(shè)計[62,74]。Zhao等[75]通過對TiN-C
u涂層進行陽極氧化處理,在表層得到了納米管結(jié)構(gòu)的TiO2涂層,在離子毒性與光催化的共同作用下
涂層展現(xiàn)出良好的防污潛力。Yi等[76]將等離子噴涂與納秒激光技術(shù)結(jié)合,制得了具有微槽仿生
結(jié)構(gòu)的TiO2涂層,該涂層在銳鈦礦光催化與仿生結(jié)構(gòu)防粘附的綜合作用下表現(xiàn)出優(yōu)異的防污性能。
鈦涂層在海洋工程材料腐蝕防護方面具有巨大的應(yīng)用潛力。覆有鈦涂層的鋼材在海水中表現(xiàn)出優(yōu)異的
耐蝕性,其在海洋防腐領(lǐng)域的工程化應(yīng)用指日可待。然而,采用金屬涂層解決生物污損問題仍是挑戰(zhàn),防
污鈦涂層的設(shè)計需在耐腐蝕、抗磨損與防污元素釋放之間綜合權(quán)衡[77],當(dāng)前防污鈦涂層材料的研究仍
處于實驗室階段,與工程化應(yīng)用仍有距離。
3.2生物醫(yī)療領(lǐng)域
鈦涂層因優(yōu)異的耐蝕與生物相容等特性在改善醫(yī)用植入體使用性能方面受到廣泛關(guān)注[3,14]。
TC4在骨植入物材料中應(yīng)用普遍,但其中V、Al元素的潛在毒性引起了人們擔(dān)憂[78]。So
noda等[79]采用PVD技術(shù)在TC4表面制備了純Ti涂層,有效阻止了毒性離子的滲出
,提高了TC4的生物相容性。鈦雖有較好的生物相容性,但生物活性差,為增強植入物與骨組織的結(jié)
合,Sun等[80]采用冷噴涂技術(shù)制備了Ti+Mg復(fù)合涂層,后以真空燒結(jié)的方式使Mg成分揮
發(fā),得到具有良
好骨整合能力的多孔Ti涂層。為進一步提高植入物表面生物活性,Guillem-MarTi等
[81]通過冷噴涂在純Ti表面制得了具有良好生物活性與骨整合能力的羥基磷灰石-Ti復(fù)合涂層。
廣州三鑫金屬科技有限公司采用真空等離子噴涂制得的覆有羥基磷灰石-Ti涂層的人工髖關(guān)節(jié)與關(guān)節(jié)面實
現(xiàn)了商業(yè)化應(yīng)用,如圖5b所示。純Ti與TC4雖耐蝕性好,但硬度低、耐磨性差。任旭輝等[
82]為提高TC4人工關(guān)節(jié)面的耐磨性,采用PVD在基體表面沉積了TiN涂層,經(jīng)測試該材
料耐磨性和磨損穩(wěn)定性都顯著優(yōu)于市場主流的CoCrMo合金關(guān)節(jié)面材料。TiN涂層因高硬度、生
物惰性等被廣泛用于金屬表面防護,但由于存在針孔、裂紋等固有缺陷,在腐蝕介質(zhì)中有基材被腐蝕的風(fēng)險
。為提升TiN涂層對基體的保護作用,Zhao等[83]采用PVD在TC4合金上制得了
Ti/TiN復(fù)合多層涂層,其中金屬Ti中間層可充當(dāng)腐蝕介質(zhì)與基體間的有效屏障,抑制TiN
柱狀晶連續(xù)生長,減少涂層針孔缺陷,提高涂層的抗裂性與耐蝕性[9,84]。該復(fù)合涂層在37℃
的模擬體液中
表現(xiàn)出優(yōu)異的耐磨蝕性能,與TC4合金和單層TiN涂層相比耐磨蝕能力分別提高了約58倍
和2倍,其磨損機制如圖7所示。
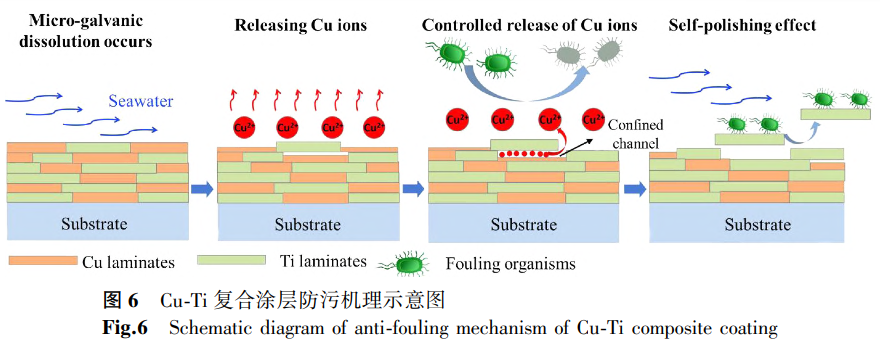
生物醫(yī)用材料在實際應(yīng)用中存在細菌感染的風(fēng)險,抗菌鈦涂層材料可在保有基體力學(xué)性能的基礎(chǔ)上賦予
植入體良好的抗菌性。Jin等[85]采用磁控濺射技術(shù)在316L不銹鋼表面制備了具有優(yōu)異耐
蝕與耐磨性能的Ti-Cu涂層,經(jīng)測試該涂層表現(xiàn)出優(yōu)異的抗菌性(99.9%)。季震宇等[86]
采用磁控濺射技術(shù)在Ti表面制備了Ti-ZnO復(fù)合涂層,發(fā)現(xiàn)當(dāng)靶材拼接比例V(Ti)∶V(ZnO)=95∶5時,涂層表現(xiàn)出優(yōu)異的抗菌性。Wang等[87]采用等離子噴涂在304不銹
鋼表面制備了Ag-TiO2復(fù)合涂層,得益于TiO2光催化與Ag+抗菌的協(xié)同作用,該涂層在保
持低細胞毒性的基礎(chǔ)上展現(xiàn)出良好的抗菌性。
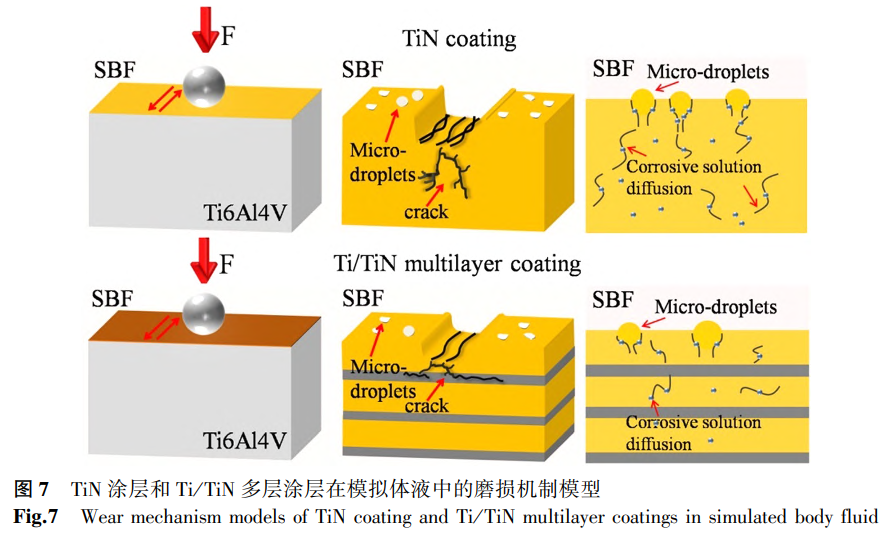
鈦涂層顯著提升了植入體的表面性能,提高了植入體的生物相容性,根據(jù)不同應(yīng)用需求選擇合適的涂層
,大大提高了材料的可選擇性,降低工程成本。抗菌鈦涂層與海洋防污
涂層具有一定相似性,都需要確保在具備抑制生物膜粘附能力的基礎(chǔ)上,使材料保有良好的耐蝕、耐磨
與力學(xué)性能,這對抗菌鈦涂層材料提出了更高的要求。
3.3航空航天領(lǐng)域
航空航天材料服役環(huán)境惡劣,對材料的耐磨、耐高溫、抗氧化腐蝕等性能要求極高。現(xiàn)有單一金屬材
料難以滿足其性能要求,表面涂層技術(shù)具有約束少、設(shè)計性強、選擇空間
大、經(jīng)濟環(huán)保等優(yōu)點,加之鈦材的獨特優(yōu)勢,使鈦涂層在航空航天材料研發(fā)領(lǐng)域得到了研究人員的重視
[88-89]。
航空航天等飛行器件需克服重力運行,輕質(zhì)金屬諸如鈦合金備受青睞,已被應(yīng)用于飛行器的各類框、梁
、機翼、發(fā)動機扇葉等部位,但鈦合金存在硬度低、耐高溫氧化能力差等
問題,進一步應(yīng)用受限[88]。鈦金屬化合物具有高硬度與高溫穩(wěn)定性,在基體表面沉積鈦金屬化
合物涂層可改善基體性能,Li等[90]采用高能機械合金法在TC4基體上制得了具有耐高溫和阻
燃特性的Ti-Cu與Ti-Cr涂層。含Al、Si等元素的鈦金屬化合物具有較好的抗高溫氧化能
力,F(xiàn)eng等[91]采用激光熔覆技術(shù)在TC4表面制備了(Ti3Al+TiB)/Ti涂
層,并通過加入3%LaB6,借助其吸氧、細化晶粒與彌散強化的作用,使熔覆鈦涂層的耐磨性與抗
高溫氧化性得以提升;為降低材料成本,Sun等[21]以Ti粉、Si粉和蔗糖為原料,采用噴霧
造粒/前驅(qū)體熱解技術(shù)制得Ti-Si-C復(fù)合粉末,然后使用該粉末,通過反應(yīng)等離子噴涂在TC4基
體上得到了室溫與高溫(600℃)耐磨性分別相當(dāng)于基體170倍和40倍的鈦涂層材料。航空
發(fā)動機葉片在沙塵、海洋高濕等惡劣環(huán)境下高速運轉(zhuǎn)時,葉片表層會受到風(fēng)沙顆粒、高溫鹽霧顆粒等物質(zhì)的
侵蝕作用。曹鑫等[92]在TC4合金表面制得了多層梯度TiN/Ti涂層,該復(fù)合涂層有著高
硬度與良好的抵抗裂紋萌生、擴展能力,大大提高了葉片抗沖蝕性能;Li等[9]在TC11合金表
面制得了TiN/Ti多層涂層,研究了其耐高溫?zé)岣g能力,發(fā)現(xiàn)相較于單層TiN涂層,TiN/Ti多層涂層可顯著提升基材的抗熱鹽腐蝕性能。除鈦合金外,鎂合金、鋁合金因其低密度與優(yōu)異的
力學(xué)性能在航空航天材料中也有所應(yīng)用,這兩類材料同樣存在耐蝕與耐磨性差等問題,對其進行鈦涂層改性
可提高基體服役性能。楊镕菲等[93]采用PVD技術(shù)在2A12鋁合金基體表面制得了耐蝕性為
基體2倍的鈦涂層,Xie等[94]采用PVD技術(shù)在AZ31鎂合金基體上制備了耐磨損性能
優(yōu)異的Ti/TiN涂層。鈦涂層已在航空發(fā)動機、直升機引擎螺旋槳葉片等結(jié)構(gòu)中得到了實際應(yīng)用
,如圖5c所示[95]。
鈦涂層的應(yīng)用大大改善了航空航天輕質(zhì)金屬耐磨、耐高溫與耐蝕等性能差的問題,該領(lǐng)域材料服役環(huán)境
惡劣,對鈦涂層性能有著極高要求。對鈦涂層成分進行調(diào)控,以及開發(fā)
多層復(fù)合鈦涂層,將有助于材料服役性能的進一步提升,促進航空航天材料性能革新。
3.4其他領(lǐng)域
除了上述應(yīng)用領(lǐng)域外,基于鈦涂層的優(yōu)異特性,其在能源化工、機械加工、汽車制造等行業(yè)也有研究涉
及[10,13,39]。
在能源化工領(lǐng)域,考慮到鈦對酸、堿、鹽等腐蝕介質(zhì)具有耐蝕性,曲彥平等[13]采用電弧噴涂在
Q235鋼表面制備了純Ti涂層,封孔后的涂層在60℃下的60%濃硫酸中表現(xiàn)出優(yōu)異的耐蝕
性。Golkovski等[96]采用激光熔覆在鈦合金基體表面制得了對沸騰濃硝酸有著優(yōu)異耐蝕作
用的Ti-Ta基合金涂層材料。隨著技術(shù)的發(fā)展,高耐蝕、低成本的鈦涂層材料有望應(yīng)用于濃縮塔、冷
凝器、反應(yīng)釜等化工設(shè)備中[64]。在汽車零件制造與機械加工領(lǐng)域,諸如發(fā)動機中齒輪、活塞零部件
與用于車銑削金屬的刀具等材料長期工作在高溫、高應(yīng)力與摩擦環(huán)境中,對材料的高溫穩(wěn)定性與耐磨性提出
了極高要求。高硬度與高溫穩(wěn)定性的鈦金屬化合物涂層可實現(xiàn)對零部件性能的提升。TiN是第一種實
現(xiàn)產(chǎn)業(yè)化并廣泛應(yīng)用的硬質(zhì)涂層,結(jié)合氣相沉積技術(shù),通過元素摻雜可得到耐高溫氧化與耐磨性能更加優(yōu)異
的硬質(zhì)涂層。上海英屹涂層技術(shù)有限公司制備的覆有TiAlN的金屬鉆頭實現(xiàn)了工業(yè)化應(yīng)用,如圖5
d所示,同時如TiAlN、TiSiN、TiBN等硬質(zhì)涂層也具有很好的應(yīng)用價值[10]。基于
鈦材料的優(yōu)異特性,加之技術(shù)的不斷進步,相信在不久的將來,鈦涂層會在不同工程領(lǐng)域中發(fā)揮更大價值。
4、結(jié)語與展望
鈦及其合金因優(yōu)異性能備受關(guān)注,但鈦材加工難、成本高等問題限制了其廣泛應(yīng)用。為充分利用鈦材
特性并降低材料成本,在基體表面沉積鈦涂層是一種有效方法。本文介紹了鈦涂層常用制備技術(shù),包括噴
涂技術(shù)、激光熔覆技術(shù)、氣相沉積技術(shù),并概述了進一步提高涂層性能的常用后處理方法。此外,還著重
對鈦涂層在海洋工程、生物醫(yī)療、航空航天
等領(lǐng)域的應(yīng)用研究現(xiàn)狀進行了綜述。
目前國內(nèi)外鈦涂層研究中存在的問題主要包括:
①制備研究多集中在工藝參數(shù)調(diào)控方面,對顆粒沉積結(jié)
合機理研究較少,同時鈦涂層制備時也會面臨氧化問題;
②鈦涂層在不同的基體上會出現(xiàn)力學(xué)、電化學(xué)等性
能不匹配等問題,對鈦涂層在不同材料上的適應(yīng)性問題報道較少;
③海洋防污與生物抗菌方面有著一定的相
似性,兩個領(lǐng)域的鈦涂層開發(fā)具有一定的相互借鑒意義,但對鈦涂層用于海洋防污的研究報道較少。針對
這些問題,未來鈦涂層材料的發(fā)展趨勢可歸納為以下幾方面。
(1)新材料的設(shè)計與優(yōu)化:在鈦涂層制備領(lǐng)域,可通過改變元素種類與含量等變量,開展高通量實驗
,同時根據(jù)不同材料的優(yōu)勢,進行多層復(fù)合結(jié)構(gòu)涂層開發(fā),以尋求新型鈦涂
層材料,改善性能并降低成本。
(2)制備工藝技術(shù)創(chuàng)新:結(jié)合目前鈦涂層研究所反映出的問題,改進制備設(shè)備與提升工藝技術(shù),在提
高效率、降低成本與減少環(huán)境影響的前提下,提高鈦涂層的質(zhì)量和性能。
(3)結(jié)合計算機與人工智能技術(shù)實現(xiàn)定制化應(yīng)用:針對工程應(yīng)用需求,將實驗、有限元模擬與機器學(xué)
習(xí)相結(jié)合,進行制備工藝過程仿真,以期獲得低成本且滿足定制化服役需求
的鈦涂層材料。
參考文獻
1LiuC,ZhangYH,LiuJF,etal.OceanEngineer
ingEquipmentandTechnology,2021,8(2),75(inCh
inese).
劉存,張有慧,劉俊斐,等.海洋工程裝備與技術(shù),2021,8(2),75.
2TianLM,YinY,BingW,etal.JournalofBioni
cEngineering,2021,18(2),239.
3LiWY,CaoC,YinS.ProgressinMaterialsSci
ence,2020,110,100633.
4MeghwalA,AnupamA,MurtyBS,etal.Journal
ofTHermalSprayTechnology,2020,29(5),857.
5LiuYN,DingY,YangLJ,etal.JournalofMan
ufacturingProcesses,2021,66,341.
6LuX.Titaniumpowdernearnetformingtechnol
ogy,MetallurgicalIndus-tryPress,China,2022,pp
.1(inChinese).
路新.鈦粉末近凈成形技術(shù),冶金工業(yè)出版社,2022,pp.1.
7ZhaoZP.StudyontHeproperTiesofTi/steel
cladplatepreparedbycoldspraying-rollingmethod
.Ph.D.THesis,UniversityofScienceandTech-nolo
gyofChina,China,2020(inChinese).
趙志坡.冷噴涂-軋制制備鈦/鋼復(fù)合板及其性能研究.博士學(xué)位論文,中國科學(xué)技術(shù)大學(xué),20
20.
8LiN,WangQ,DongF,etal.Materials,2022,1
5(23),8535.
9LiRZ,WangSH,PuJB,etal.CorrosionScien
ce,2021,192,109838.
10ZengFF,QiuLC,WuLY,etal.SurfaceTechno
logy,2023,52(8),1(inChinese).
曾芳芳,邱聯(lián)昌,吳立穎,等.表面技術(shù),2023,52(8),1.
11HuangSF,ZengXL,PengZ,etal.SpecialCast
ing&NonFerrousAl-loys,2023,43(7),876(inChine
se).
黃紹服,曾祥領(lǐng),彭振,等.特種鑄造及有色合金,2023,43(7),876.
12TianJJ,XuKW,HuJH,etal.JournalofMater
ialsScience&Techno-logy,2021,79,62.
13QuYP,WangJ,WuJY,etal.MaterialsProtect
ion,2014,47(4),57(inChinese).
曲彥平,王建,吳俊宇,等.材料保護,2014,47(4),57.
14LiaoTY,BiesiekierskiA,BerndtCC,etal.P
rogressinSurfaceScience,2022,97(2),100654.
15GuoJJ,YangYF,ZhuQS,etal.SurfaceandCo
aTingsTechnology,2018,353,18.
16AngA,BerndtC.InternaTiOnalMaterialsRevi
ews,2014,59(4),179.
17CHenJQ,LiuM,DengCM,etal.HeatTreatment
ofMetals,2018,43(1),204(inChinese).
陳建強,劉敏,鄧春明,等.金屬熱處理,2018,43(1),204.
18IshikawaK,SuzukiT,KitamuraY,etal.Journ
alofTHermalSprayTech-nology,1999,8(2),273.
19VilardellAM,CincaN,Garcia-GiraltN,etal.
MaterialsScienceandEngineeringC,2020,107,110
306.
20ZhangWX,GuJP,ZhangC,etal.SurfaceandC
oaTingsTechnology,2019,358,511.
21SunX,LiW,HuangJH,etal.AppliedSurfaceS
cience,2020,508,145264.
22ZhouHX,LiCX,LiCJ.ChinaSurfaceEngineer
ing,2020,33(2),1(inChinese).
周紅霞,李成新,李長久.中國表面工程,2020,33(2),1.
23GuliziaS,TrenTinA,VezzùS,etal.In:THerm
alSpray2010:Procee-dingsfromtHeInternaTiOnal
THermalSprayConFerence.Singapore,2010,
pp.80.
24PozaP,Garrido-ManeiroMá.ProgressinMateri
alsScience,2022,123,100839.
25GardonM,LatorreA,TorrellM,etal.Materia
lsLetters,2013,106,97.
26WongW,IrissouE,RyabininA,etal.Journalo
fTHermalSprayTech-nology,2011,20(1),213.
27MacDonaldD,RahmaTiS,JodoinB,etal.Journ
alofTHermalSprayTechnology,2019,28(1),161.
28LiWY,CaoCC,WangGQ,etal.ScienceandTec
hnologyofWeldingandJoining,2019,38(3),337.
29PanJM,SunYF,LiuXH,etal.PracTicalsurf
aceengineeringmanual,ChinaMachinePress,China
,2018,pp.843(inChinese).
潘繼民,孫玉福,劉新紅,等.實用表面工程手冊,機械工業(yè)出版社,2018,pp.84
3.
30WuZJ,WuZJ,ZengKL,etal.ModerntHermals
prayingtechnology,ChinaMachinePress,China,20
18,pp.11(inChinese).
吳子健,吳朝軍,曾克里,等.現(xiàn)代熱噴涂技術(shù),機械工業(yè)出版社,2018,pp.11.
31XieZY,LiuCS,WuQ,etal.SurfaceTechnolog
y,2023,52(7),25(inChinese).
謝志穎,劉常升,吳瓊,等.表面技術(shù),2023,52(7),25.
32WangC,LiJJ,WangT,etal.SurfaceandCoaTi
ngsTechnology,2021,416,127137.
33WangP,YeYS.AppliedLaser,2018,38(3),377
(inChinese).
王培,葉源盛.應(yīng)用激光,2018,38(3),377.
34MaW,XuX,XieYS,etal.SurfaceandCoaTings
Technology,2024,477,130383.
35WangZW.PreparaTiOnprocessandproperTieso
fTitaniumandTitaniumal-loycoaTingsbyplasmacl
adding.Master’sTHesis,UniversityofScienceand
TechnologyBeijing,China,2019(inChinese).
王志煒.等離子熔覆鈦及鈦合金涂層制備工藝及性能研究.碩士學(xué)位論文,北京科技大學(xué),201
9.
36ZhuLD,XuePS,LanQ,etal.OpTics&LaserTe
chnology,2021,138,106915.
37XiaoY,XiongJ,GuoZX,etal.JournalofCent
ralSouthUniversity,2020,27(3),721.
38ChoyKL.ProgressinMaterialsScience,2003,
48(2),57.
39JinN,YangYQ,LuoX,etal.ProgressinMater
ialsScience,2013,58(8),1490.
40DengY,CHenWL,LiBX,etal.CeramicsIntern
aTiOnal,2020,46,18373.
41KimHJ,OdoulS,LeeCH,etal.SurfaceandCo
aTingsTechnology,2001,140(3),293.
42LuoXT,WeiYK,WangY,etal.Materials&Des
ign,2015,85,527.
43ZhaoZP,TariqNH,TangJR,etal.Materials
&Design,2020,185,108249.
44LiWY,ZhangC,GuoX,etal.AdvancedEnginee
ringMaterials,2007,9(5),418.
45MolakRM,ArakiH,WatanabeM,etal.Journal
ofTHermalSprayTechnology,2015,24(8),1459.
46ZhuWY.EfFectofsealingtreatmentoncorros
ionresistanceoftHermalsprayedmetalbasecoaTin
gs.Master’sTHesis,YangzhouUniversity,Chi-na,2
021(inChinese).
朱無言.封孔處理對熱噴涂金屬涂層耐腐蝕性能影響研究.碩士學(xué)位論文,揚州大學(xué),2021.
47ShiZP,WangZB,QiaoYX.MaterialsScience&
EngineeringTechno-logy,2020,51(11),1507.
48DengW,HouGL,LiSJ,etal.UltrasonicsSono
cHemistry,2018,44,115.
49MorończykB,Ura-BińczykE,KurodaS,etal.Sur
faceandCoaTingsTechnology,2019,363,142.
50BiSQ,XuKW,ShaoGS,etal.JournalofMater
ialsScience&Tech-nology,2023,159,125.
51GaoYK.SurfaceEngineering,2006,22(4),299
.
52LiuJY,LuoXT,WanP,etal.THermalSprayTe
chnology,2023,15(4),1(inChinese).
劉建禹,雒曉濤,萬鵬,等.熱噴涂技術(shù),2023,15(4),1.
53XiaoH,LiuX,LuQH,etal.JournalofMateria
lsResearchandTech-nology,2022,19,2981.
54FaksaL,DavesW,EckerW,etal.InternaTiOna
lJournalofRefractoryMetalsandHardMaterials,
2019,82,174.
55ZhouHX,LiCX,JiG,etal.JournalofAlloys
andCompounds,2018,766,694.
56XiongTY,WangJQ.ActaMetallurgicaSinica,
2023,59(4),537(inChinese).
熊天英,王吉強.金屬學(xué)報,2023,59(4),537.
57LiZM,YangXP,ZhangJB,etal.AdvancedEng
ineeringMaterials,2016,18(7),1240.
58ZhaoZP,TangJR,TariqNH,etal.Materials
ScienceandEngineeringA,2020,795,139982.
59ZhaoZP,TariqNH,TangJR,etal.Materials
ScienceandEngineeringA,2020,775,138968.
60ZhaiYJ,LiuXB,QiaoSJ,etal.SurfaceTech
nology,2017,46(6),207(inChinese).
翟永杰,劉秀波,喬世杰,等.表面技術(shù),2017,46(6),207.
61UllahI,SiddiquiMA,LiuH,etal.ACSBiomat
erialsScience&Engi-neering,2020,6(3),1355.
62JinHC,TianLM,BingW,etal.ProgressinMa
terialsScience,2022,124,100889.
63LiZY,WangN,LiSH,etal.CoaTings,2023,1
3(11),1894.
64BaiYL,LiuXF,WangWJ,etal.ChineseJourn
alofEngineering,2021,43(1),85(inChinese).
白于良,劉雪峰,王文靜,等.工程科學(xué)學(xué)報,2021,43(1),85.
65WuLK,GuoPJ,ZHengL,etal.SurfaceTechnol
ogy,2022,51(5),79(inChinese).
伍廉奎,郭蒲俊,鄭磊,等.表面技術(shù),2022,51(5),79.
66WangZZ,HuangGS,XingLK,etal.TitaniumI
ndustryProgress,2020,37(2),7(inChinese).
王治中,黃國勝,邢路闊,等.鈦工業(yè)進展,2020,37(2),7.
67魯宏,戴魏魏,蔣倩,等.中國專利,CN115627470A,2023.
68HaiMN,HuangF,WangYM.MetalWorld,2021,3
7(5),16(inChinese).
海敏娜,黃帆,王永梅.金屬世界,2021,37(5),16.
69GuZJ,SuFT,ZhangZG,etal.Corrosion&Pro
tecTiOn,1999,20(4),166(inChinese).
辜志俊,蘇方騰,張志剛,等.腐蝕與防護,1999,20(4),166.
70RomeuMJ,Mergulh?oF.Microorganisms,2023,
11(6),1568.
71SelimMS,YangH,WangFQ,etal.RSCAdvances
,2018,8(18),9910.
72ZhaiXF,JuP,GuanF,etal.SurfaceandCoaTi
ngsTechnology,2020,397,125959.
73ShaJN,LiuX,CHenRR,etal.JournalofColl
oidandInterfaceScience,2023,637,67.
74RichardsC,SlaimiA,O’ConnorN,etal.Inter
naTiOnalJournalofMo-leCularSciences,2020,21(1
4),5063.
75ZhaoY,WangCT,HuJM,etal.CeramicsIntern
aTiOnal,2021,47(5),7233.
76YiP,JiaHY,YangXS,etal.ColloidsandSur
facesA:PhysicocHemi-calandEngineeringAspects,
2023,656,130357.
77YuY,XuNN,ZhuSY,etal.JournalofMateria
lsScience&Technolo-gy,2021,69,48.
78VeigaC,DavimJP,LoureiroAJR.ReviewsonA
dvancedMaterialsScience,2012,32,133.
79SonodaT,SaitoT,WatazuA,etal.Surfaceand
InterfaceAnalysis,2006,38(4),797.
80SunJF,HanY,CuiK.MaterialsLetters,2008,
62(21),3623.
81Guillem-MarTiJ,CincaN,PunsetM,etal.Coll
oidsandSurfacesB:Biointerfaces,2019,180,245.
82RenXH,ZhouML,ZHenZX,etal.ChinaMedica
lEquipment,2022,19(12),21(inChinese).
任旭輝,周夢林,鄭照縣,等.中國醫(yī)學(xué)裝備,2022,19(12),21.
83ZhaoCL,ZhuYB,YuanZW,etal.SurfaceandC
oaTingsTechnology,2020,403,126399.
84KrellaAK.SurfaceandCoaTingsTechnology,2
013,228,115.
85JinXM,GaoLZ,LiuEQ,etal.JournaloftHe
MechanicalBehaviorofBiomedicalMaterials,2015,
50,23.
86JiZY,MaX,LiuP,etal.MaterialsProtecTiO
n,2023,56(2),1(inChinese).
季震宇,馬迅,劉平,等.材料保護,2023,56(2),1.
87WangQ,TangZL,HeroutR,etal.Surfacesand
Interfaces,2024,45,103856.
88WangX,LuoXK,YuB,etal.AeronauTicalManu
facturingTechnology,2022,65(4),14(inChinese)
.
王欣,羅學(xué)昆,宇波,等.航空制造技術(shù),2022,65(4),14.
89JiMM,ZhuSZ,MaZ.SurfaceTechnology,2021
,50(1),253(inChinese).
姬梅梅,朱時珍,馬壯.表面技術(shù),2021,50(1),253.
90LiB,DingRD,SHenYF,etal.Materials&Des
ign,2012,35,25.
91FengYQ,F(xiàn)engK,YaoCW,etal.Materials&De
sign,2019,181,107959.
92CaoX,HeWF,WangSG,etal.ChinaSurfaceEn
gineering,2021,34(3),120(inChinese).
曹鑫,何衛(wèi)鋒,汪世廣,等.中國表面工程,2021,34(3),120.
93YangRF,LiX,SunQX,etal.HeatTreatment,
2021,36(1),6(inChinese).
楊镕菲,李想,孫啟軒,等.熱處理,2021,36(1),6.
94XieWL,ZhaoYM,LiaoB,etal.SurfaceandCo
aTingsTechnology,2022,441,128590.
95YuanFH,ZhangJP,CHengYX,etal.AeronauTi
calManufacturingTechnology,2016(S1),40(inChi
nese).
袁福河,張佳平,程玉賢,等.航空制造技術(shù),2016(S1),40.
96GolkovskiMG,SamoylenkoVV,PolyakovIA,et
al.JournalofPhy-sics:ConFerenceSeries,2018,1
115(4),042045.
萬福程,北京科技大學(xué)工程技術(shù)研究院碩士研究生,在路新研究員的指導(dǎo)下進行研究。目前主要研究
領(lǐng)域為海洋防污鈦涂層。
路新,通信作者,北京科技大學(xué)工程技術(shù)研究院研究員、博士研究生導(dǎo)師,國家優(yōu)秀青年基金獲得者。
目前主要從事注射成形與增材制造等先進金屬粉末近凈成形技術(shù)、先進粉末冶金材料模擬計算及優(yōu)化設(shè)計方
法、生物醫(yī)用鈦合金材料制備與表征等方面的研究工作。
無相關(guān)信息