采用輕質高強材料可有效降低航空航天裝備總質量并提升服役水平。超高強鈦合金具有高比強度和優異的耐腐蝕性能及抗疲勞性能,成為先進航空航天裝備關鍵承力構件的首選材料[1-3],如應用于BOEING777飛機起落架的Ti-1023鈦合金[4]和應用于AIRBUS350飛機起落架的Ti-5553鈦合金[5]等亞穩β型鈦合金。
超高強高韌鈦合金的熱處理制度通常為β單相區固溶處理和時效析出,通過形成魏氏組織的方式提升鈦合金的蠕變抗力、斷裂韌性和抗裂紋擴展能力,并有效抑制鈦合金在兩相區加工過程中誘發的微觀組織不均勻性[6-8]。但是由于β相具有較高的層錯能,如果固溶處理制度設置不合理,極易造成β晶粒快速長大甚至異常長大,形成粗大的β晶粒組織,導致強度和塑性顯著下降,無法滿足微觀組織與力學性能間的協調匹配[9-10]。此外,固溶后的冷卻過程中可能發生溶質元素脫溶析出形成α相,可能引發鈦合金微觀組織和力學性能的變化[11-12]。近期,我國開發了一種新型超高強韌TB18鈦合金,其名義成分為Ti-5Al-5Mo-5V-6Cr-1Nb-0.5Fe[13],然而,針對TB18鈦合金熱處理強韌化的相關研究報道較少。
為獲得與性能需求相匹配的微觀組織,明確超高強高韌TB18鈦合金的固溶處理工藝參數,闡明超高強高韌TB18鈦合金熱處理工藝-微觀組織-力學性能間的交互作用關系,以兩相區成形的TB18鈦合金棒材為研究對象,研究固溶溫度、固溶時間和固溶冷速對TB18鈦合金微觀組織和力學性能的影響規律,給出超高強高韌鈦合金TB18的最佳固溶處理工藝參數,以期為超高強高韌TB18鈦合金批量化生產提供合理的熱處理制度。
1、實驗
采用西部超導材料科技股份有限公司提供的α+β兩相區鍛造后制備成的TB18鈦合金Φ400mm棒材,化學成分如表1所示,α+β/β轉變點溫度為(800±5)℃。初始兩相態TB18鈦合金包含初生相αp和β基體,如圖1a所示,初生相αp均勻分布于β基體中,呈球狀或粗棒狀。在β基體中還包含大量片層狀次生相αs和細針狀αs,如圖1b所示。
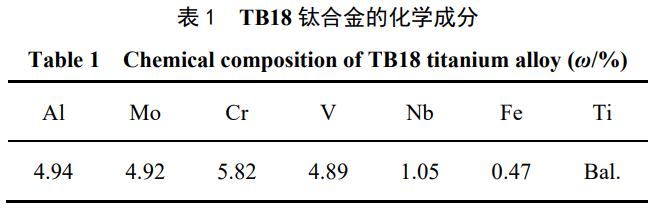
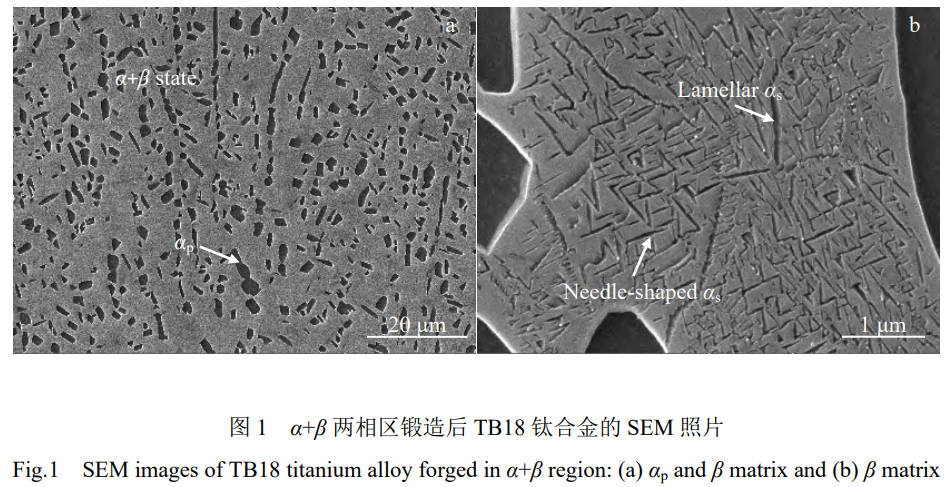
熱處理試驗采用Φ400mm×80mm規格TB18鈦合金試樣片,設計不同固溶溫度、固溶時間和固溶后冷卻速率的熱處理強韌性匹配試驗,工藝參數和試驗流程如圖2a~2c所示,時效處理制度統一為530℃×4h,AC。采用Zwick/RoellZ100型萬用拉伸機進行室溫拉伸試驗,試驗標準GB/T228.1,拉伸試樣長度與方向與試樣片軸線方向平行,標距段長度為25mm,直徑5mm。采用Zwick/RoellRPK300型夏比擺錘沖擊試驗機進行室溫沖擊試驗,試驗標準GB/T229,沖擊試樣長度方向與試樣片軸線方向平行,總長55mm,寬度10mm。采用MTSLandmark370.25高頻疲勞試驗機進行平面應變斷裂韌性(KIC)測試,試驗標準GB/T4161,KIC樣品方形面與試樣片平面平行,寬度62.5mm,厚度25mm,缺口寬度3mm。每組室溫拉伸、室溫沖擊和平面應變斷裂韌度試驗重復3次后取平均值。采用奧林巴斯光學顯微鏡(optical microscope,OM)和JEOLIT700型場發射掃描電鏡(scanning electron microscope,SEM)對材料的相組成、相形貌、相分布進行觀測。采用配置于JEOLIT700型場發射SEM上的OxfordC-Nano型電子背散射衍射(electron back scattere ddiffraction,EBSD)系統進行晶體取向和結構表征,采用FEITalosF200X型場發射透射電子顯微鏡(transmission electron microscope,TEM)獲得材料的兩相界面、位錯等微觀組織結構信息,用于闡明TB18鈦合金熱處理工藝-微觀組織-力學性能間的交互作用關系。
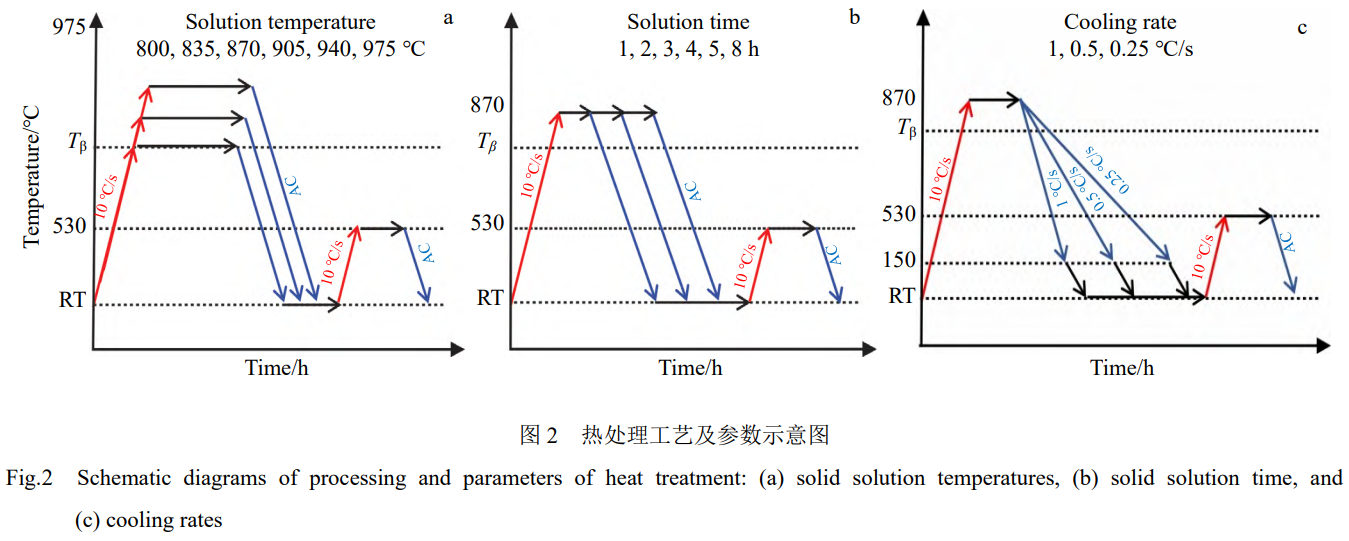
2、結果與討論
2.1固溶溫度對TB18鈦合金組織和性能的影響
經過不同固溶溫度處理并時效后的TB18鈦合金室溫拉伸和室溫沖擊試驗結果如圖3所示。圖3a中綠線代表TB18鈦合金目標抗拉強度1280MPa,紫線代表TB18鈦合金目標屈服強度1180MPa,圖3b中粉線代表TB18鈦合金目標塑性延伸率5%,藍線代表TB18鈦合金目標沖擊韌性25J/cm2。當固溶溫度由800℃提升至975℃,經過530℃×4h,AC時效處理后的TB18鈦合金的抗拉強度由1378MPa逐漸降低至1252MPa,呈線性下降趨勢。當固溶溫度由800℃提升至870℃時,延伸率和沖擊韌性分別由3.3%和18.4J/cm2提升至8.5%和29.2J/cm2,此時材料的強度和韌性滿足超高強高韌TB18鈦合金的需求,即抗拉強度≥1280MPa,屈服強度≥1180MPa,延伸率≥5%,沖擊韌性≥25J/cm2。繼續增加固溶溫度,材料的延伸率和沖擊均呈現下降趨勢。
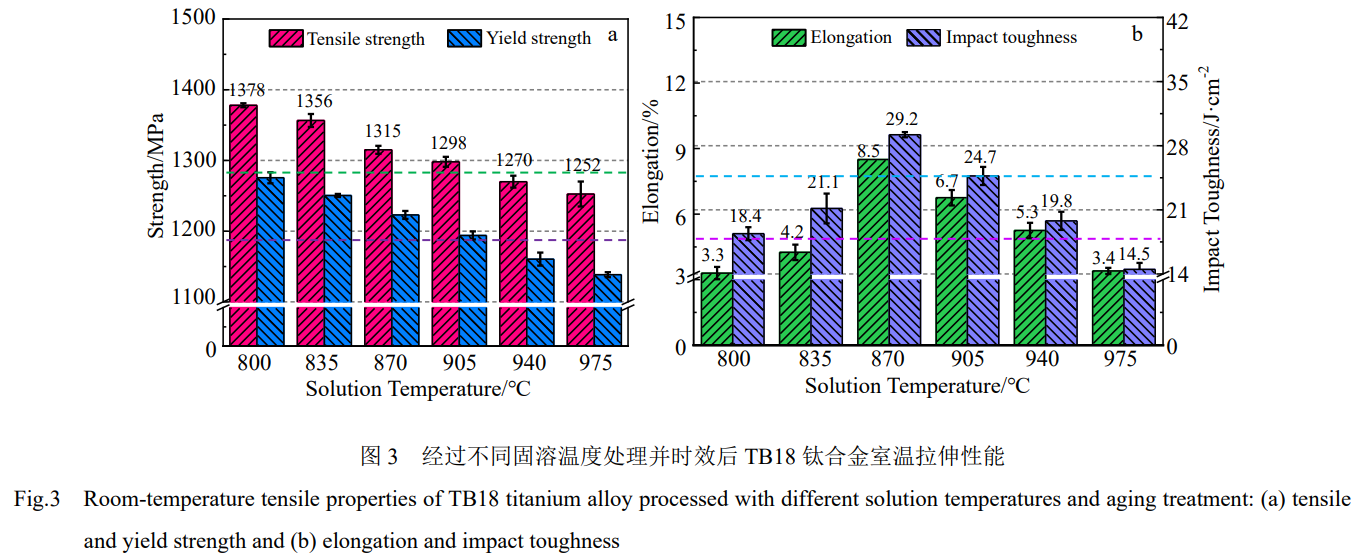
表2列出TB18鈦合金經不同溫度固溶保溫并在530℃×4h,AC時效后的斷裂韌度KIC值。當固溶溫度在835~905℃時,時效后TB18鈦合金的斷裂韌度均大于超高強高韌鈦合金的標準值65MPa·m1/2。當固溶溫度為835℃時,TB18鈦合金的斷裂韌度為(75.6±0.7)MPa·m1/2;提升固溶溫度至870℃后,斷裂韌度值為(88.4±1.5)MPa·m1/2;繼續提升溫度至905℃后,斷裂韌度值為(95.7±0.6)MPa·m1/2。
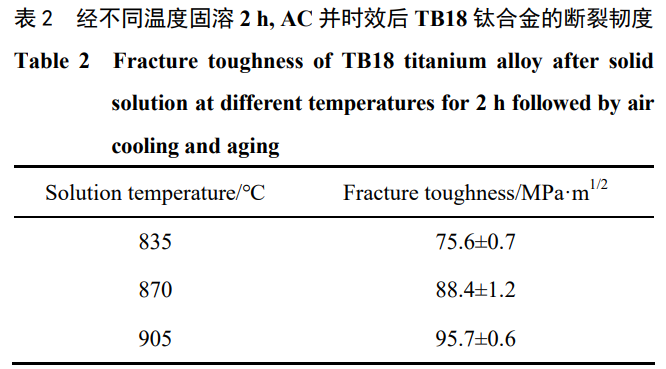
圖4給出了經過835、870、940和975℃固溶2h空冷后的TB18鈦合金的OM照片,經過β單相區固溶后TB18鈦合金的晶粒均呈等軸狀。隨固溶溫度的提升,TB18鈦合金的平均晶粒尺寸由150μm提升至335μm,表明提升固溶溫度有利于TB18鈦合金發生靜態再結晶引發晶粒的均勻長大,晶粒的晶界相對平直,多條晶界匯集時在二維觀察面中形成120°穩定三叉晶界。此外,當固溶溫度由835℃提升至870℃后,平均晶粒尺寸增加10μm;當固溶溫度由940℃提升至975℃后,平均晶粒尺寸增加90μm,表明在相同固溶時間條件下,β單相區固溶溫度越高,越有利于β晶粒的長大粗化。
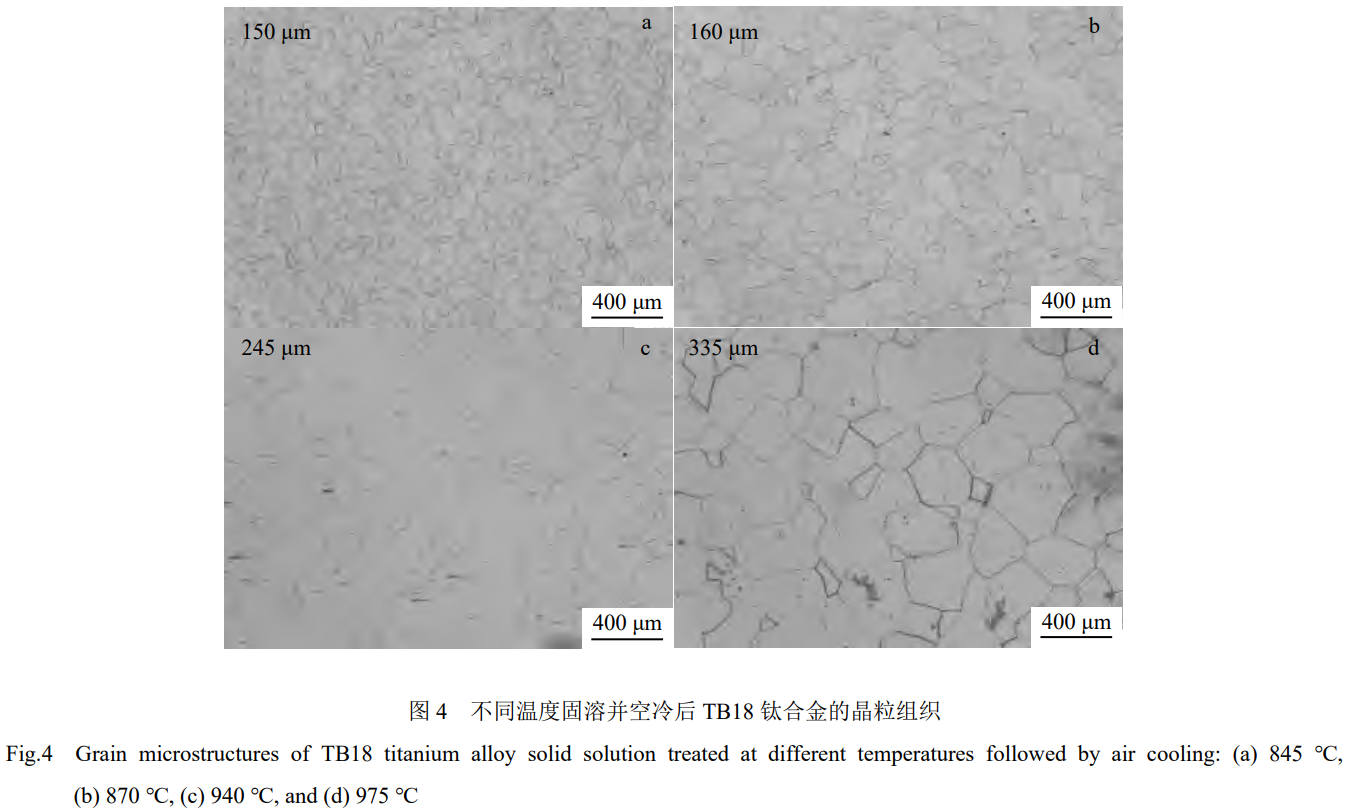
依據Hall-Patch關系,增加β單相區固溶溫度引發的晶粒長大導致材料強度下降。此外,在800℃固溶后平均晶粒尺寸較小,提供了更多有利于元素擴散的錯配程度相對較高的晶界,時效過程中部分元素優先在此處聚集,使晶界相粗化,降低材料的塑性和韌性。提升固溶溫度后,一方面材料在靜態再結晶作用下發生晶粒長大,降低材料強度;另一方面,晶界錯配程度降低,晶界相擴散形核難度增加,材料的塑性提升[14]。因此,當固溶溫度由800℃提升至870℃時,TB18鈦合金強度降低但是塑性和韌性逐漸提高。當固溶溫度超過870℃,TB18鈦合金的平均晶粒尺寸快速增長,使材料強度降低的同時,可提供TB18鈦合金位錯交滑移的界面減少,使材料的塑性和韌性降低。綜上所述,適用于制備超高強高韌TB18鈦合金的β單相區固溶溫度為870℃。
經過時效處理后TB18鈦合金中元素分布如圖5所示。β基體中析出大量片層和針狀αs相,如圖5a所示。Al元素均勻分布,如圖5b所示。時效后TB18鈦合金中還分布有Mo、V和Cr的β穩定元素,如圖5c~5e所示,可以向TB18鈦合金提供固溶強化效果[15-16]。中性元素Nb均勻分布,如圖5f所示。
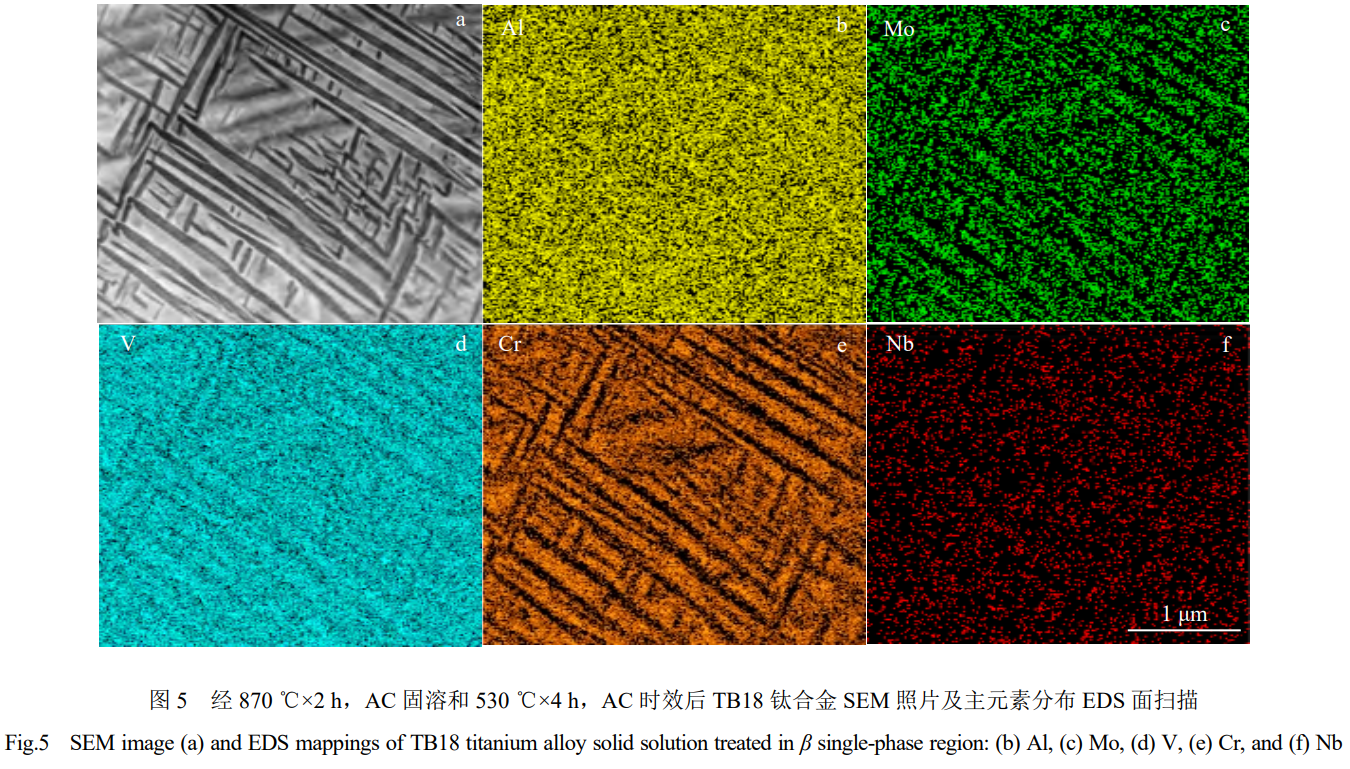
如圖6a,6b所示,經過870℃×2h,AC固溶和530℃×4h,AC時效處理后TB18鈦合金的β基體中析出了大量片層和針狀αs,長度為100nm~5μm,寬度小于200nm。這些αs相互之間平行或呈一定夾角,表明與β基體存在強烈的Burgers關系[17]。時效后TB18鈦合金承受塑性變形時,位錯需繞過或切過這些相和兩相界面,變形抗力增加,因此形成了強烈的強化效果。當固溶溫度提高至905℃,TB18鈦合金的β基體中同樣析出了彌散分布的片層和針狀αs相,但是部分αs相發生粗化,如圖6c,6d所示。可能的原因是固溶后冷卻過程中析出少量αs相,并在時效后發生粗化,表明TB18鈦合金在β單相區固溶時,提升固溶溫度會輕度影響αs相的尺寸與形貌。
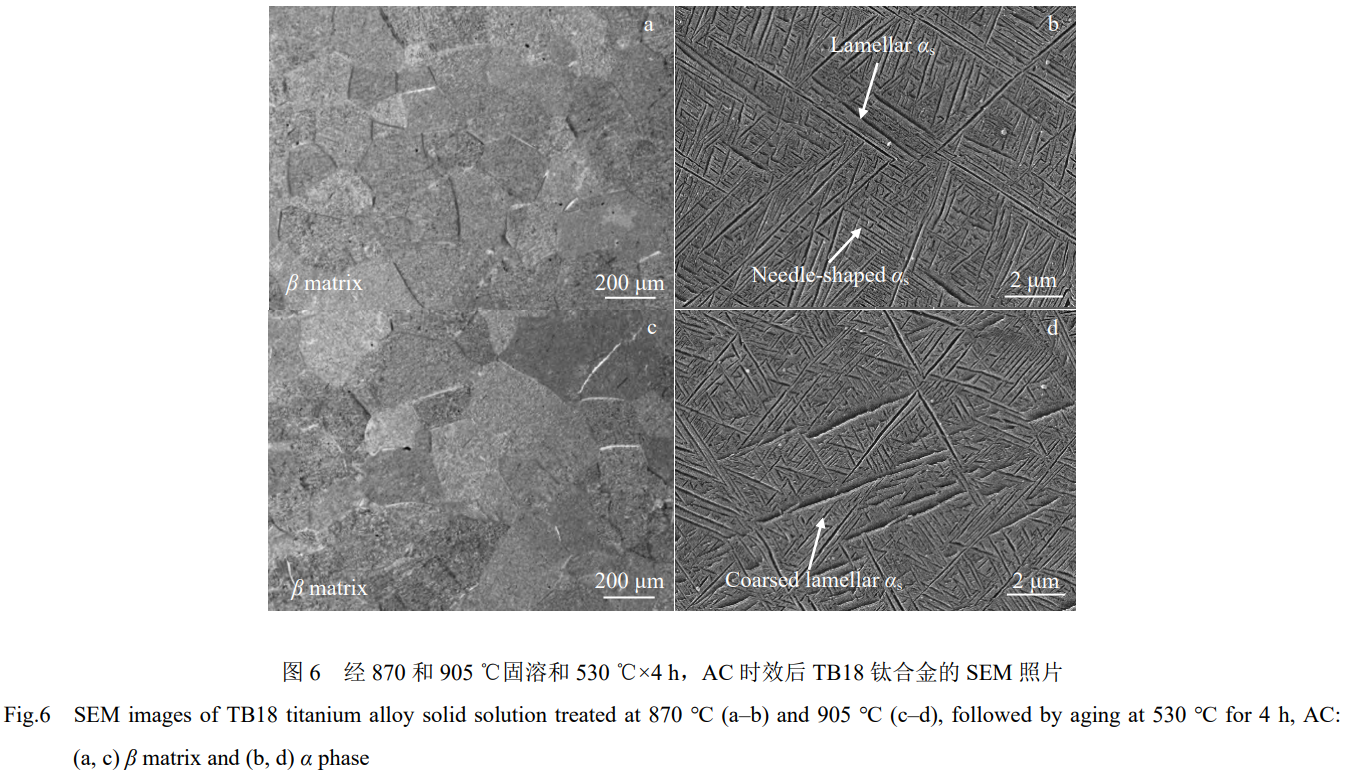
Liu等人[18]通過Ti-55511鈦合金的熱處理試驗,認為近β型鈦合金的晶粒尺寸粗化和片層αs相的粗化可以提升近β型鈦合金的斷裂韌性。由于TB18鈦合金固溶溫度引發β晶粒粗化和片層αs相粗化,并且形成典型魏氏組織,有效阻礙了裂紋拓展的路徑,因此通過提升固溶溫度,可以有效提升TB18鈦合金的斷裂韌性。
圖7展示了經870℃×2h,AC固溶和530℃×4h,AC時效后TB18鈦合金晶內αs相和晶界αs相的SEM照片和EBSD結果。如圖7a~7c所示,晶內hcp結構片層αs相與bcc結構的β基體存在取向關系,相間KAM值較小,界面較為穩定。晶界αs相片層厚度(約1μm)略大于晶界兩側αs相,相內KAM值較小,而晶界兩側αs相取向差較大,處亞穩狀態。如果發生后續塑性變形,位錯容易在晶界αs相界面快速累積[19-20],因此晶界αs相會弱化材料的塑性和韌性。
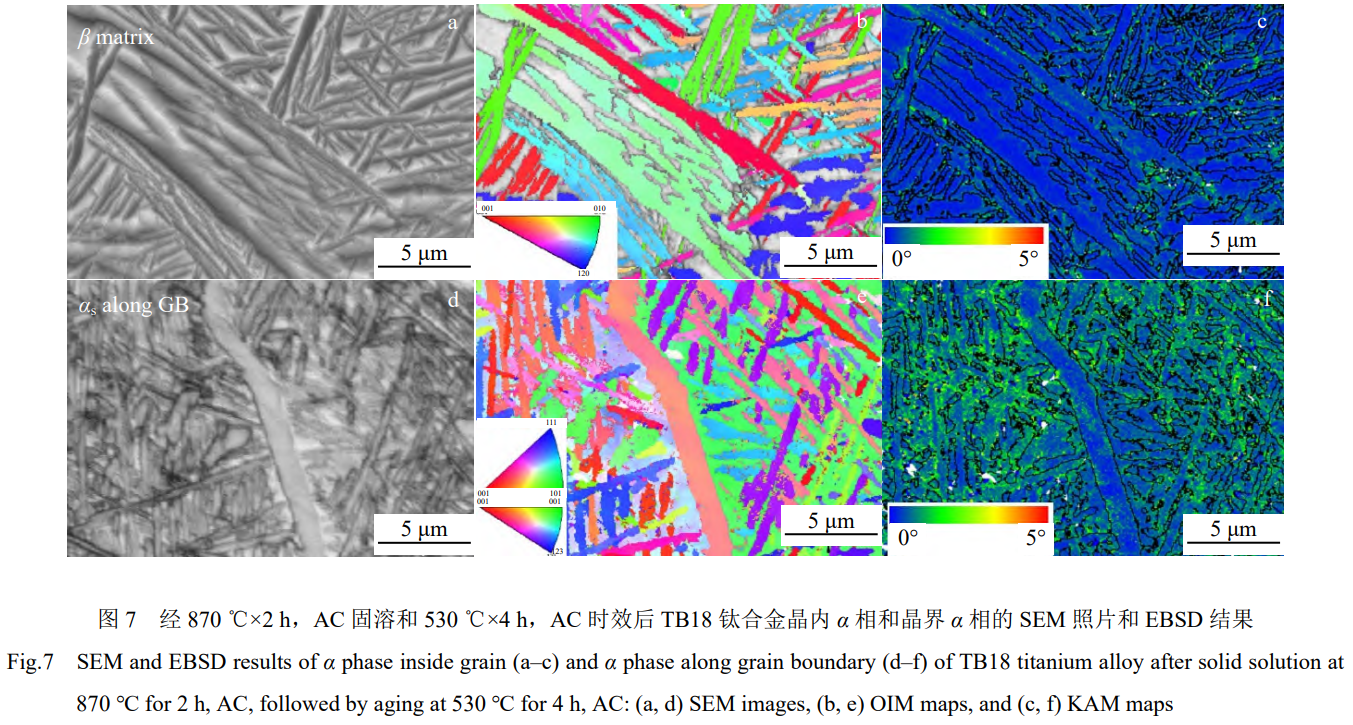
圖8給出了經870℃×2h,AC固溶和530℃×4h,AC時效后TB18鈦合金的晶界附近典型形貌TEM照片。獲取選區電子衍射(selected area electron diffraction,SAED)和高分辨TEM(high-resolution transmission electron microscopy,HRTEM)時電子束入射角為[110]β。由圖8a~8e可知,經熱處理后TB18鈦合金晶界附近存在大量相互平行且較長的片層αs相束集,與晶界垂直分布,呈典型魏氏組織分布形貌[21-22]。這種晶界處生成的魏氏組織可以釘扎位錯[23-24],有利于提高TB18鈦合金強度。
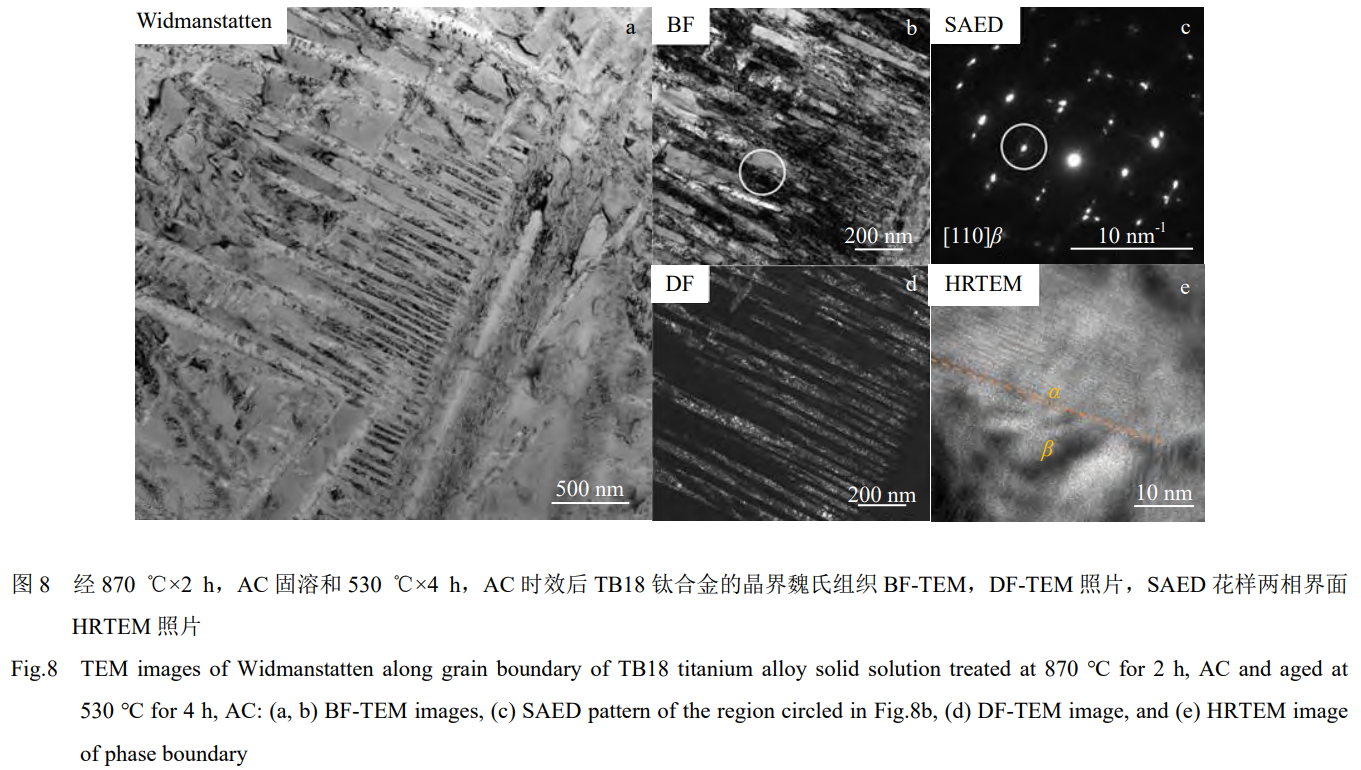
2.2固溶時間對TB18鈦合金組織與性能的影響
固溶保溫時間是決定鈦合金固溶度的因素之一。為保證試樣片充分預熱,應保證TB18鈦合金在固溶溫度下保溫充足的時間;同時,如果TB18鈦合金在β單相區固溶時間過長,容易導致β晶粒粗化。如圖9a,9b所示,當TB18鈦合金在870℃固溶4h,AC后,平均晶粒尺寸為255μm,相比于870℃×2h,AC樣品,晶粒尺寸增加95μm;當固溶時間延長至8h,平均晶粒尺寸為380μm,晶粒顯著粗化,不利于TB18鈦合獲得良好的塑性和韌性。
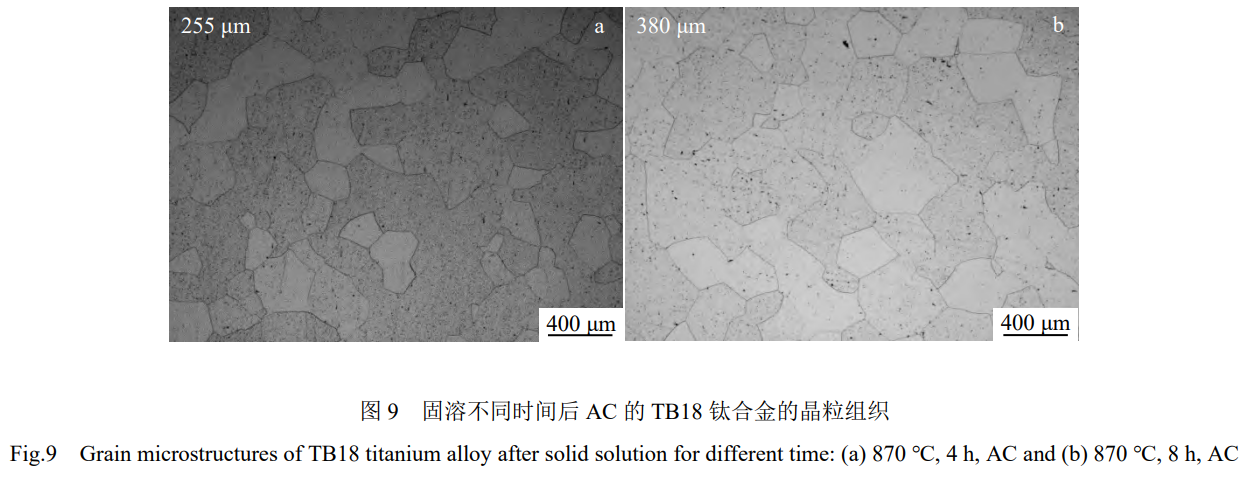
圖10給出了經過870℃固溶不同時間后AC并經過530℃×4h,AC時效處理后的TB18鈦合金的力學性能。由圖10a可知,TB18鈦合金在β單相區固溶并時效后的強度對固溶時間有關聯性。由于試樣片直徑和厚度較大,固溶時間為1h時試樣片未完全熱透,固溶度相對較低,無法獲得充分時效析出強化效果。同時由于固溶時間短,材料內靜態再結晶程度相對較低,鍛造時殘余的位錯并未完全通過再結晶的方式耗散,在后續變形中容易達到斷裂失效的臨界值,降低材料的塑性和韌性。延長固溶時間至2h,試樣片完全熱透,固溶度較高,時效析出強化效果好,此時,TB18鈦合金時效后的抗拉強度為1315MPa、屈服強度1225MPa,延伸率為8.5%、沖擊韌性為29.2J/cm2,滿足超高強高韌TB18鈦合金的性能需求。繼續延長固溶時間,TB18鈦合金的強度、塑性和韌性均發生下降,主要由于固溶時間增加后TB18鈦合金在熱激活作用下發生靜態再結晶,β晶粒尺寸顯著增加后導致強度和塑韌性下降。綜上所述,當固溶時間為2h時,TB18鈦合金的強度和塑韌性匹配值最高。
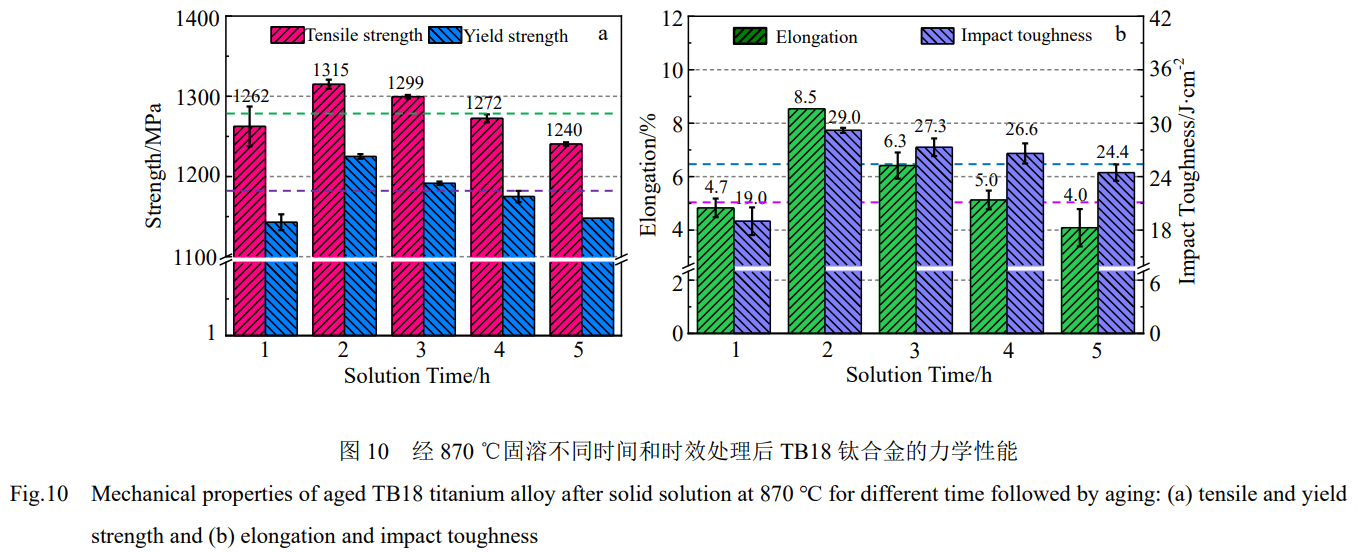
2.3固溶冷速對TB18鈦合金組織與性能的影響
0.25℃/s時,TB18鈦合金的β晶粒中析出了大量細密的針狀αs相,如圖11a,11d所示。這是由于固溶后冷卻過程中,TB18鈦合金經歷了αs相的析出區間,當冷速率較低時,產生了與時效處理類似的析出沉淀效果,因此在不經過時效處理的條件下就獲得了較為細密的αs相,但是存在少量無析出區(precipitates-freeregion)。固溶冷卻速率提升至0.5℃/s后,同樣析出了αs相,但是β晶粒內部無析出區占比增加,如圖11b,11e所示。這是由于冷速增加后TB18固溶冷卻后經過αs相析出溫度區間的時間減少,為αs相析出提供的熱驅動能量減少,抑制了αs相的析出。當固溶冷卻速率提升至1℃/s后,晶界無析出區的占比繼續增加,僅在晶內和晶界析出了部分αs相,如圖11e,11f。
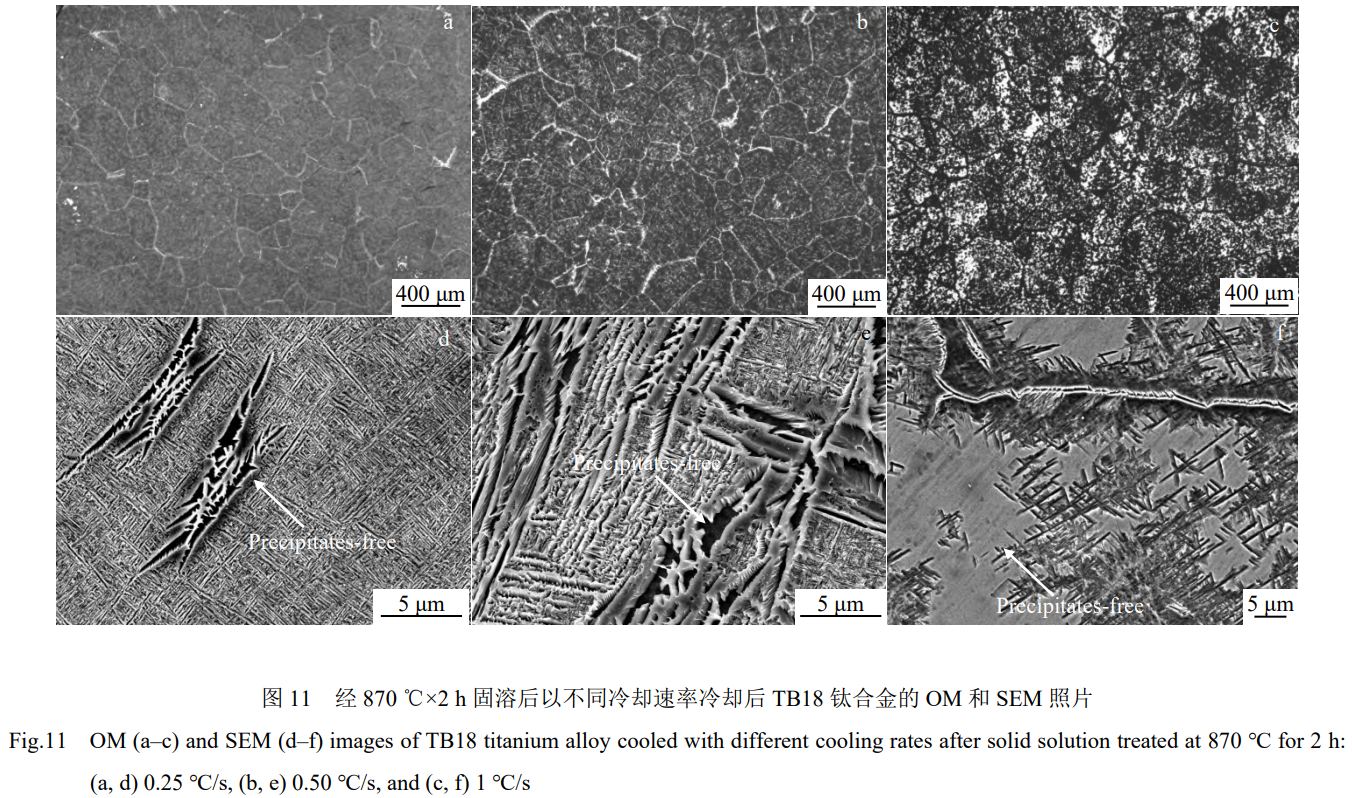
圖12給出了經870℃固溶2h后以不同冷卻速率爐冷至150℃并經過530℃×4h,AC時效處理后TB18鈦合金的力學性能。圖13為對應的組織形貌。由圖12a可知,當TB18鈦合金固溶后以0.25℃/min爐冷并時效后的強度較低為1180MPa,這是由于部分低速緩冷過程中析出的αs相嚴重粗化,呈板條狀,如圖13a,13d所示。雖然通過時效處理消除了β晶粒內部無析出區,但是部分緩冷過程中析出的αs相進一步吸收形核點附近的溶質Al元素,發生長大和粗化,導致αs相尺寸不均勻,圖11給出了經870℃固溶2h后以不同冷卻速率爐冷至150℃后TB18鈦合金的組織形貌。當固溶冷速為不利于TB18鈦合金獲得優異的強度。當固溶冷速提升至0.5℃/min后,TB18鈦合金通過時效析出獲得了良好的強度,但是塑性降低,如圖13b,13e所示。當固溶冷速進一步提升至1℃/min后,原始緩冷組織中的無析出區中均析出了細小彌散的針狀次生αs相,如圖13c,13f所示,使TB18鈦合金抗拉強度提升至1343MPa,屈服強度達到1179MPa,延伸率則降低至5.0%。
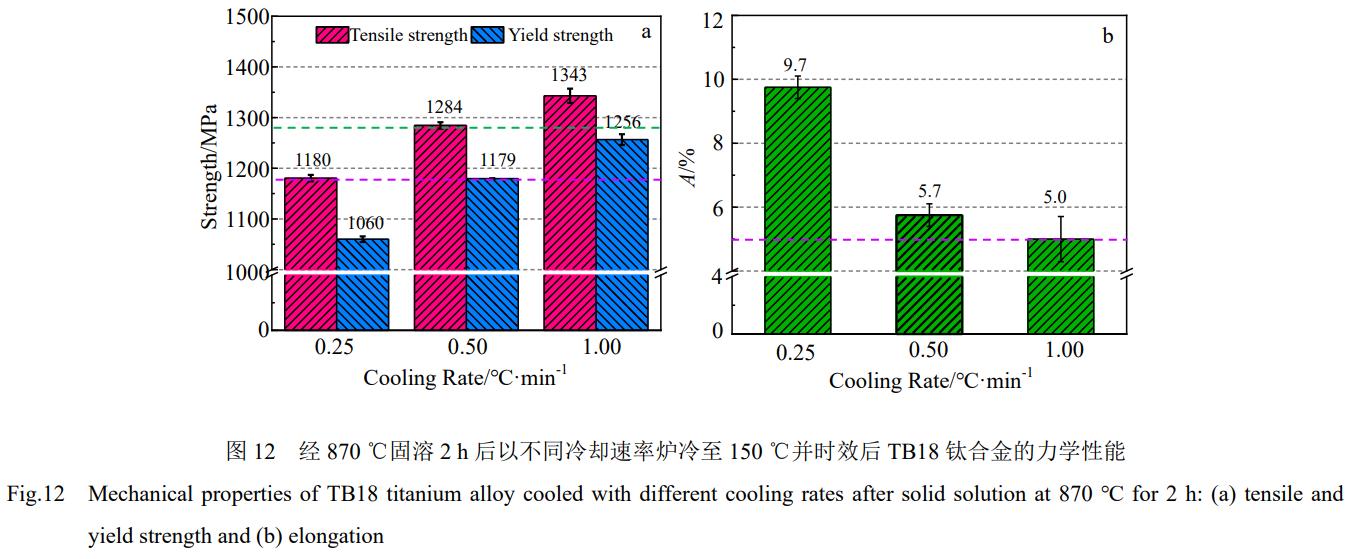
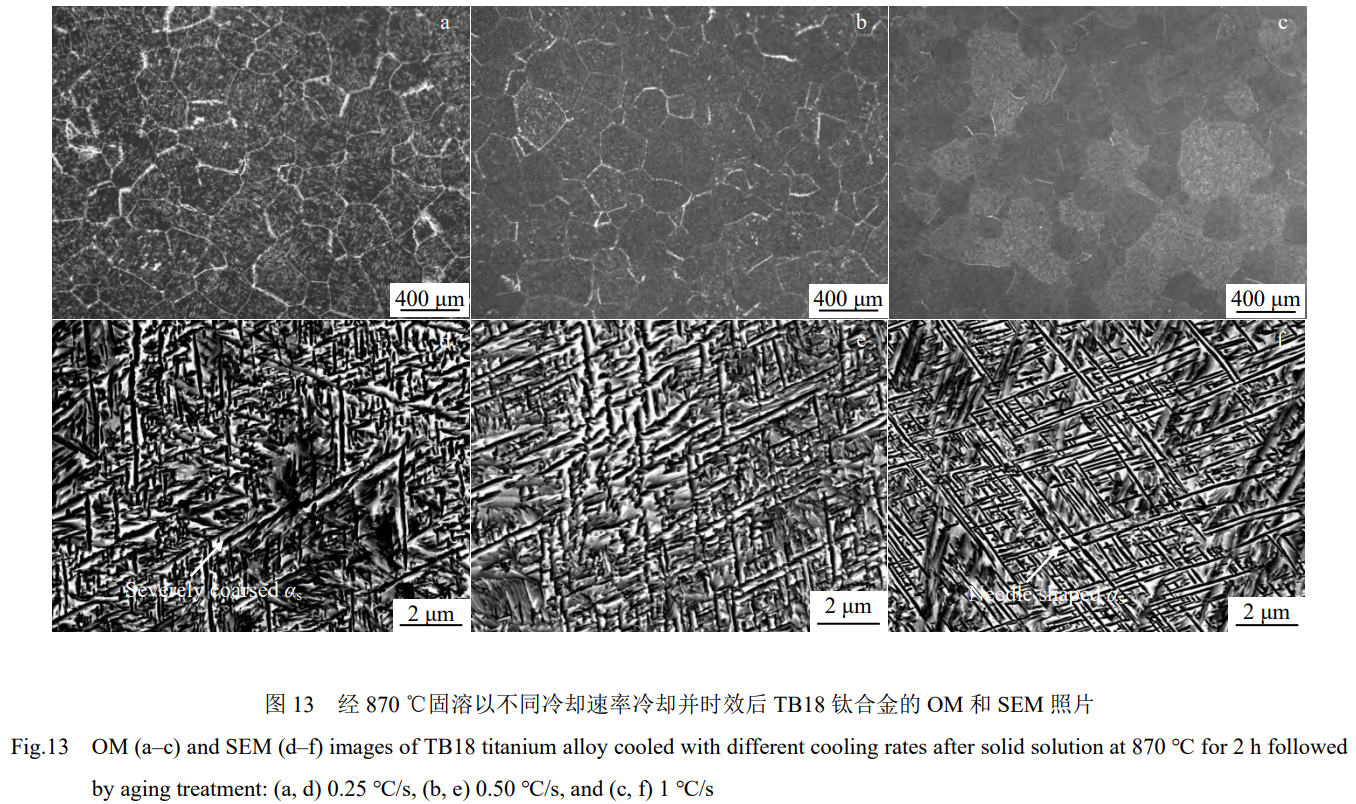
3、結論
1)通過β單相區固溶和時效處理后,TB18鈦合金中β基體中析出片層和針狀αs相,使TB18鈦合金獲得良好的析出強化效應。形成的片層狀αs相有利于提升TB18鈦合金的韌性,片層厚度越大,TB18鈦合金的斷裂韌性越好。
2)TB18鈦合金在β單相區固溶后形成亞穩等軸β晶粒,且晶粒尺寸與固溶溫度和固溶時間相關。固溶溫度過高或固溶保溫時間過長將導致TB18鈦合金β晶粒發生粗化,使材料強度和塑性下降。當固溶制度為870℃×2h,AC時,TB18鈦合金可在530℃×4h,AC條件下時效后獲得良好的強韌性匹配,抗拉強度為1315MPa,屈服強度為1225MPa,延伸率為8.5%,沖擊韌性為29.2J/cm2,斷裂韌度值為88.4MPa·m1/2。
3)固溶后冷卻速率影響TB18鈦合金的力學性能。當固溶后TB18鈦合金以0.25℃/min冷卻至150℃后,β基體中已經析出了大量αs相,同時存在少量無析出區。經過530℃×4h,AC時效后無析出區消失,部分αs相明顯粗化,TB18鈦合金抗拉強度降低為1180MPa。提升固溶冷速至1℃/min后,經870℃固溶的TB18鈦合金在未時效前存在大量無析出區,但是在530℃×4h,AC時效后獲得了均勻細密的αs相,抗拉強度提高達到1343MPa,延伸率為5.0%。
參考文獻References
[1] Lu K. Science[J], 2010, 328(5976): 319
[2] Zhang X Y, Zhao Y Q, Bai C G. Titanium Alloys and Applications[M]. Beijing: Chemical Industry Press, 2005
[3] Cotton J D, Briggs R D, Boyer R R et al. JOM[J], 2015, 67(6): 1281
[4] Guo Hongzhen(郭鴻鎮), Yao Zekun(姚澤坤), Lan Fang(蘭 芳) et al. Rare Metal Materials and Engineering(稀有金屬材料與工 程)[J], 2000, 29(6): 408
[5] Boyer R R, Briggs R D. Journal of Materials Engineering and Performance[J], 2005, 22: 2916
[6] Ivasishin O M, Markovsky P E, Matviychuk Y V et al. Journal of Alloys and Compounds[J], 2008, 457(1): 296
[7] Qin D Y, Zhao F, Li Y L. Materials Science and Engineering A[J], 2022, 841: 143074
[8] Zhao Q Y, Sun Q Y, Xin S W et al. Materials Science and Engineering A[J], 2022, 845: 143260
[9] Sadeghpour S, Javaheri V, Abbasi S M et al. Physica B: Condensed Matter[J], 2020, 593: 412315
[10] Gao J H, Rainforth W M. Metallurgical and Materials Transactions A[J], 2020, 51(8): 3766
[11] Shi X H, Zeng W D, Long Y et al. Journal of Alloys and Compounds[J], 2017, 727: 555
[12] Huang C W, Wang F M, Wen X et al. Journal of Materials Science[J], 2021, 56(14): 8848
[13] Li Shaoqiang(李少強), Gong Zhanpeng(弓站朋), Li Hui(李 輝) et al. Rare Metal Materials and Engineering(稀有金屬材料與工 程)[J], 2020, 49(9): 3045
[14] Zhou W, Liu X H, Feng J et al. Rare Metal Materials and Engineering[J], 2022, 51(9): 3129
[15] Ma F C, Lu W J, Qin J N et al. Materials Science and Engineering A[J], 2006, 416(1): 59
[16] Zhu X J, Fan Q B, Gong H C et al. Materials Science and Engineering A[J], 2021, 825: 141907
[17] Zhu W G, Lei J, Tan C S et al. Materials & Design[J], 2019, 168: 107640
[18] Liu Y, Lim S C V, Ding C et al. Journal of Materials Science & Technology[J], 2022, 97: 101
[19] Wang S Z, Xu S, Xiang C C et al. Materials Characterization[J], 2022, 192: 112219
[20] Qi P, Li B L, Wei W et al. Journal of Materials Research and Technology[J], 2022, 21: 429
[21] Zhao Y Q, Wu C, Wang H. Rare Metal Materials and Engineering[J], 2022, 51(12): 4389
[22] Cheng F, Wang H M, Yang J W et al. Materials Letters[J], 2023, 333: 133591
[23] Salib M, Teixeira J, Germain L et al. Acta Materialia[J], 2013, 61(10): 3758
[24] Dixit S, Kumar D, Dash B B et al. Journal of Alloys and Compounds[J], 2022, 927: 166897
無相關信息