鈦合金憑借高強(qiáng)度、低密度、優(yōu)良耐腐蝕性與生物相容性等特性,在多領(lǐng)域備受青睞。早期受限于加工技術(shù),應(yīng)用拓展緩慢。3D 打印技術(shù)興起后,為鈦合金加工開辟新路徑,其能將鈦合金材料按數(shù)字化模型逐層堆積,制造復(fù)雜形狀部件,突破傳統(tǒng)加工局限。近年來,科研人員持續(xù)攻克難題,如中國科學(xué)院金屬研究所張哲峰研究員團(tuán)隊針對3D打印鈦合金疲勞性能差的問題,發(fā)現(xiàn)打印態(tài)組織自身抗疲勞優(yōu)點被氣孔等缺陷掩蓋,進(jìn)而發(fā)明缺陷與組織分步調(diào)控新工藝,大幅提升鈦合金疲勞強(qiáng)度,推動其在航空航天等領(lǐng)域的應(yīng)用進(jìn)程 。
在3D打印耗材中,Ti6Al - 4V(TC4)是極為常見的鈦合金材質(zhì)。它以鈦為基體,融入 6% 鋁和 4% 釩,鋁可增強(qiáng)耐熱性與強(qiáng)度,釩能改善韌性與加工性。該合金密度約為鋼的 60%,比強(qiáng)度高,可制造出高強(qiáng)度、輕量化零部件,像飛機(jī)發(fā)動機(jī)部件、起落架等多有應(yīng)用。除 TC4 外,Ti6Al - 4V ELI(低間隙元素型)也用于對雜質(zhì)敏感場景,如醫(yī)療植入物;Ti - 5Al - 2.5Sn 等材質(zhì)則因自身特性,適配不同特殊需求。北京科技大學(xué)團(tuán)隊還創(chuàng)新研發(fā)出未使用傳統(tǒng)金屬合金化元素,僅靠氧元素調(diào)控組織的 HCP + FCC 雙相鈦合金,打破強(qiáng)度與塑性制衡關(guān)系 。
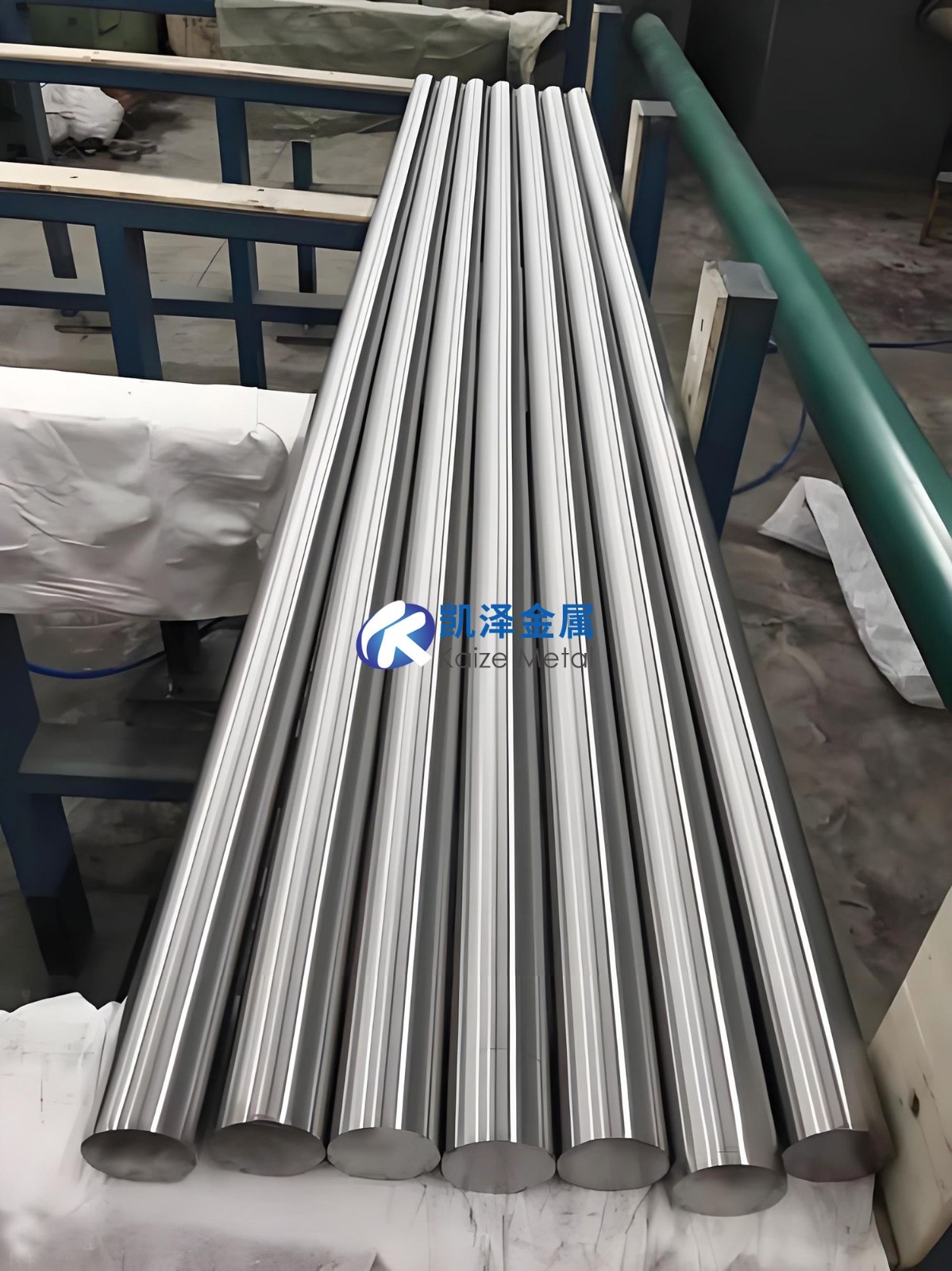
3D打印鈦合金常采用粉末床熔融、直接能量沉積、粘結(jié)劑噴射加工等工藝。以粉末床熔融為例,先通過計算機(jī)輔助設(shè)計(CAD)構(gòu)建產(chǎn)品三維模型,接著將模型切片成薄層,生成打印路徑數(shù)據(jù)。打印時,設(shè)備均勻鋪展鈦合金粉末,高能量激光或電子束按路徑逐層熔化粉末,使其凝固成型。打印完成后,需進(jìn)行后處理,如去除支撐結(jié)構(gòu)、熱處理優(yōu)化組織性能、表面處理提升表面質(zhì)量等。在航空航天領(lǐng)域制造復(fù)雜空心結(jié)構(gòu)航空零部件時,該工藝能一次性成型,減少加工工序與成本 。
行業(yè)內(nèi)已建立一系列規(guī)范3D打印鈦合金材料與制品的標(biāo)準(zhǔn)。國內(nèi)有相關(guān)國家標(biāo)準(zhǔn)對鈦合金粉末粒度分布、氧含量、松裝密度等關(guān)鍵指標(biāo)明確規(guī)定,確保粉末質(zhì)量穩(wěn)定;對打印制品的尺寸精度、內(nèi)部缺陷、力學(xué)性能等也有對應(yīng)檢測與評判標(biāo)準(zhǔn)。國際上,如 ASTM 等標(biāo)準(zhǔn)組織制定的標(biāo)準(zhǔn)在全球廣泛應(yīng)用,涵蓋從材料特性測試方法到不同行業(yè)應(yīng)用規(guī)范等多方面。在醫(yī)療植入物制造中,嚴(yán)格遵循標(biāo)準(zhǔn)才能保障產(chǎn)品安全性與有效性,滿足人體使用要求 。
未來,3D 打印鈦合金技術(shù)將聚焦降本增效與性能提升。一方面,研發(fā)新型打印設(shè)備與工藝,提高打印速度與精度,降低設(shè)備與材料成本;另一方面,深入探索材料微觀結(jié)構(gòu)與性能關(guān)系,開發(fā)高性能、多功能鈦合金材料,如兼具超高溫穩(wěn)定性與高韌性的合金。隨著技術(shù)進(jìn)步,其應(yīng)用領(lǐng)域?qū)⒉粩嗤貙挘谙M電子領(lǐng)域,蘋果、三星等企業(yè)已嘗試采用鈦合金3D打印技術(shù)制造手機(jī)中框等部件,未來有望在更多產(chǎn)品類型中普及;在醫(yī)療領(lǐng)域,個性化定制植入物將更加精準(zhǔn)高效,為患者帶來更好治療體驗 。
1. 主流鈦合金牌號與性能對比
合金牌號 | 材料類型 | 適用工藝 | 關(guān)鍵性能參數(shù) | 成本 ($/kg) |
Ti-6Al-4V (Gr.5) | α+β型 | SLM/EBM | 抗拉強(qiáng)度: 1100-1300 MPa | 120-150 |
延伸率: 8-12% |
Ti-6Al-4V ELI | 低間隙元素 | EBM/DED | 斷裂韌性: 70-90 MPa√m | 160-200 |
疲勞強(qiáng)度: 550 MPa |
Ti-5553 | 近β型 | LPBF | 強(qiáng)度: 1300-1450 MPa | 220-280 |
深淬透性: 150mm |
Ti-6242 | 高溫型 | DED | 耐溫: 550℃/100h | 300-350 |
蠕變強(qiáng)度: 450 MPa |
Ti-Cu | 新型合金 | SLM | 抗菌率>99.9% | 180-240 |
導(dǎo)電率: 15% IACS |
2. 粉末制備關(guān)鍵技術(shù)指標(biāo)
參數(shù) | 激光粉末床熔融(SLM) | 電子束熔融(EBM) | 等離子弧增材(WAAM) |
粒度分布 (μm) | 15-45 | 45-106 | 50-150 |
球形度 (%) | >98 | >95 | >85 |
氧含量 (ppm) | <800 | <1200 | <1500 |
流動性 (s/50g) | <25 | <30 | <35 |
空心粉率 (%) | <0.3 | <0.5 | <1.0 |
創(chuàng)新工藝:
等離子旋轉(zhuǎn)電極法(PREP):制備15-53μm細(xì)粉,空心粉率<0.1%
超聲霧化技術(shù):實現(xiàn)5-20μm超細(xì)粉,適用于微尺度打印
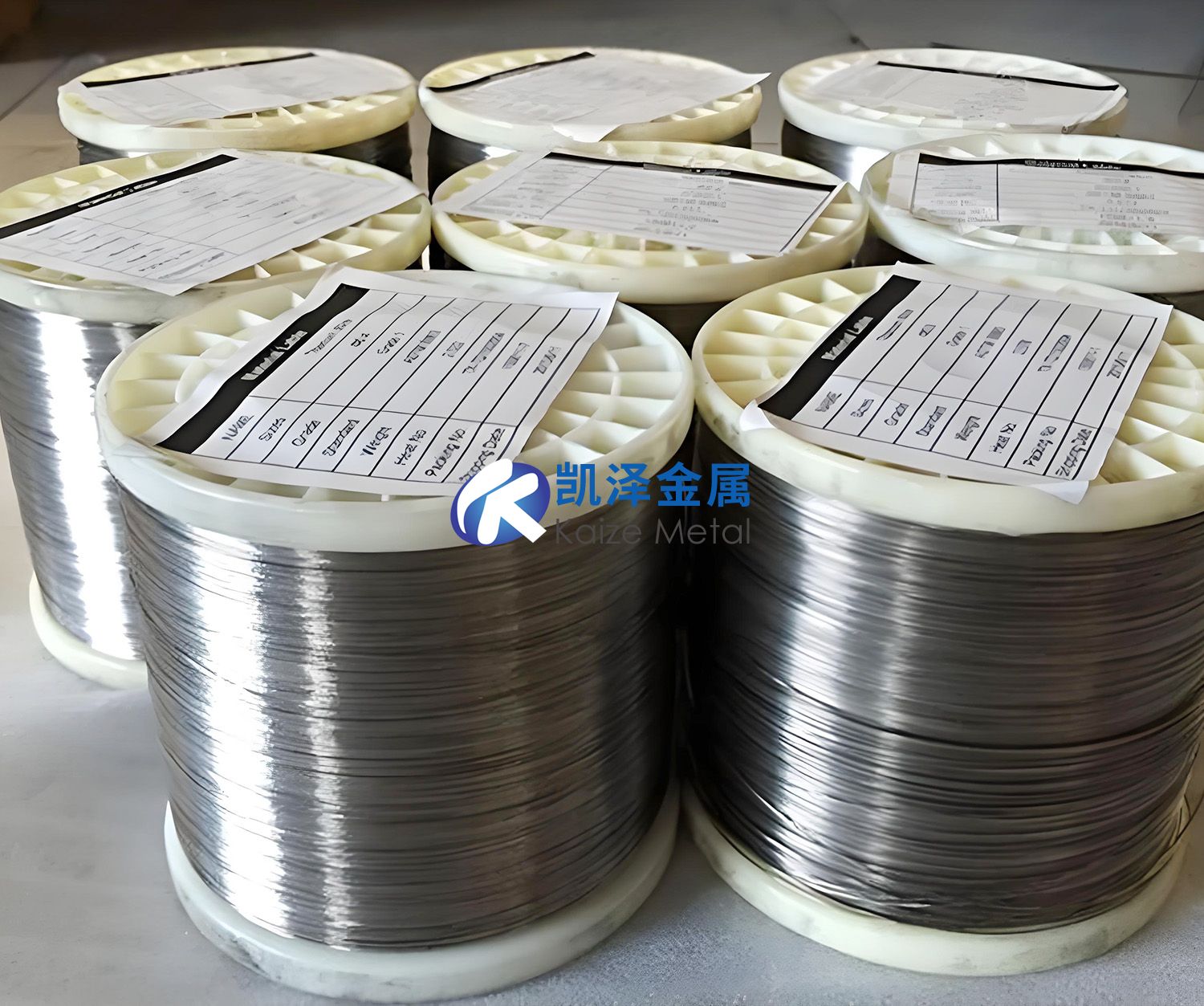
3. 工藝-組織-性能調(diào)控
工藝參數(shù) | 微觀結(jié)構(gòu)特征 | 力學(xué)性能優(yōu)化方向 |
激光功率(200-400W) | 柱狀晶/等軸晶比例 | 強(qiáng)度-韌性平衡調(diào)控 |
掃描速度(700-1400mm/s) | β晶粒尺寸(50-200μm) | 各向異性消除 |
層厚(20-60μm) | 孔隙率(0.01-0.5%) | 疲勞壽命提升 |
熱等靜壓(HIP) | α相層片厚度(0.2-1μm) | 延伸率提升至15% |
典型案例:
GE航空LEAP發(fā)動機(jī)燃油噴嘴:采用EBM Ti-6Al-4V,致密度>99.7%,減重25%,成本降低30%
史賽克骨科植入物:SLM Ti-6Al-4V ELI,孔隙率65%的多孔結(jié)構(gòu),彈性模量3GPa(接近松質(zhì)骨)
4. 行業(yè)標(biāo)準(zhǔn)與認(rèn)證體系
標(biāo)準(zhǔn)體系 | 核心要求 | 認(rèn)證難點 |
ASTM F3001 | 醫(yī)用鈦粉雜質(zhì)控制(Al/V溶出量<1μg/cm2) | 生物相容性動物實驗 |
AMS 4999 | 航空件缺陷尺寸<50μm | CT檢測分辨率要求<10μm |
ISO/ASTM 52900 | 粉末可追溯性(批次DNA編碼) | 區(qū)塊鏈存證系統(tǒng)建設(shè) |
NADCAP AC7113 | 工藝穩(wěn)定性(CPK>1.33) | 2000小時連續(xù)生產(chǎn)驗證 |
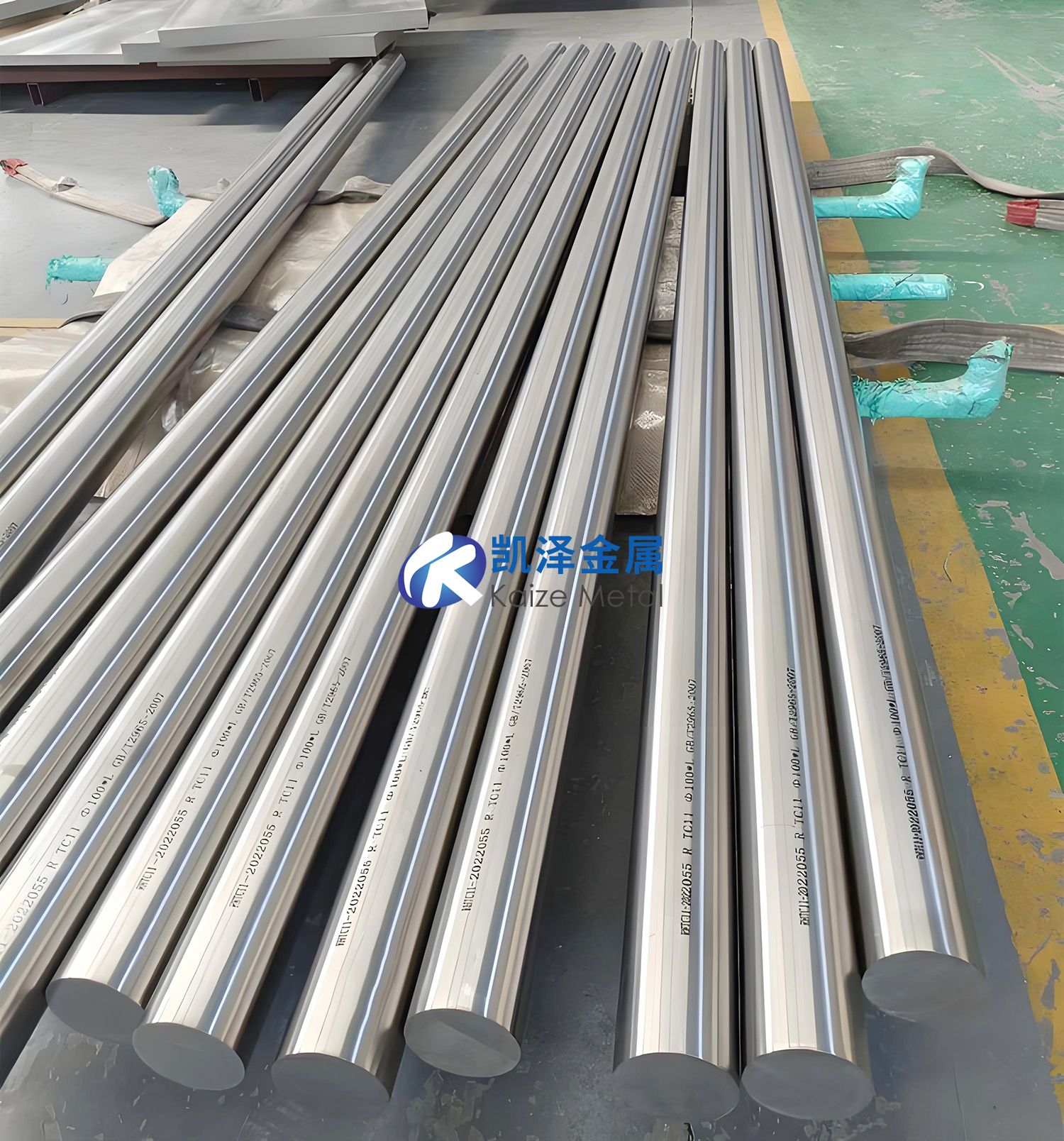
5. 技術(shù)挑戰(zhàn)與前沿突破
技術(shù)瓶頸 | 傳統(tǒng)方案 | 2023年創(chuàng)新技術(shù) | 效益提升 |
粉末成本高 | 氣霧化法(GA) | 短流程氫化脫氧(HDH) | 成本降低40% |
殘余應(yīng)力大 | 基板預(yù)熱(200℃) | 激光沖擊強(qiáng)化(LSP) | 變形量減少70% |
表面粗糙度 | 噴砂處理(Ra 8-10μm) | 電化學(xué)拋光(ECP) | Ra達(dá)0.8μm |
成分偏析 | 機(jī)械混合 | 納米包覆技術(shù)(TiB?增強(qiáng)) | 組織均勻性提升50% |
6. 應(yīng)用場景與市場數(shù)據(jù)
領(lǐng)域 | 典型部件 | 材料用量(噸/年) | 增長率 |
航空航天 | 發(fā)動機(jī)葉片/艙門鉸鏈 | 520 | 28% |
醫(yī)療 | 多孔椎間融合器/顱骨修復(fù)體 | 380 | 35% |
能源 | 燃料電池雙極板/核聚變部件 | 150 | 45% |
汽車 | 輕量化底盤結(jié)構(gòu)件 | 90 | 18% |
標(biāo)桿案例:
波音787機(jī)艙支架:WAAM工藝制造Ti-6Al-4V,生產(chǎn)周期縮短60%,材料利用率達(dá)85%
西門子燃?xì)廨啓C(jī)燃燒室:SLM Ti-6242,耐溫能力提升至600℃,熱效率提高3%
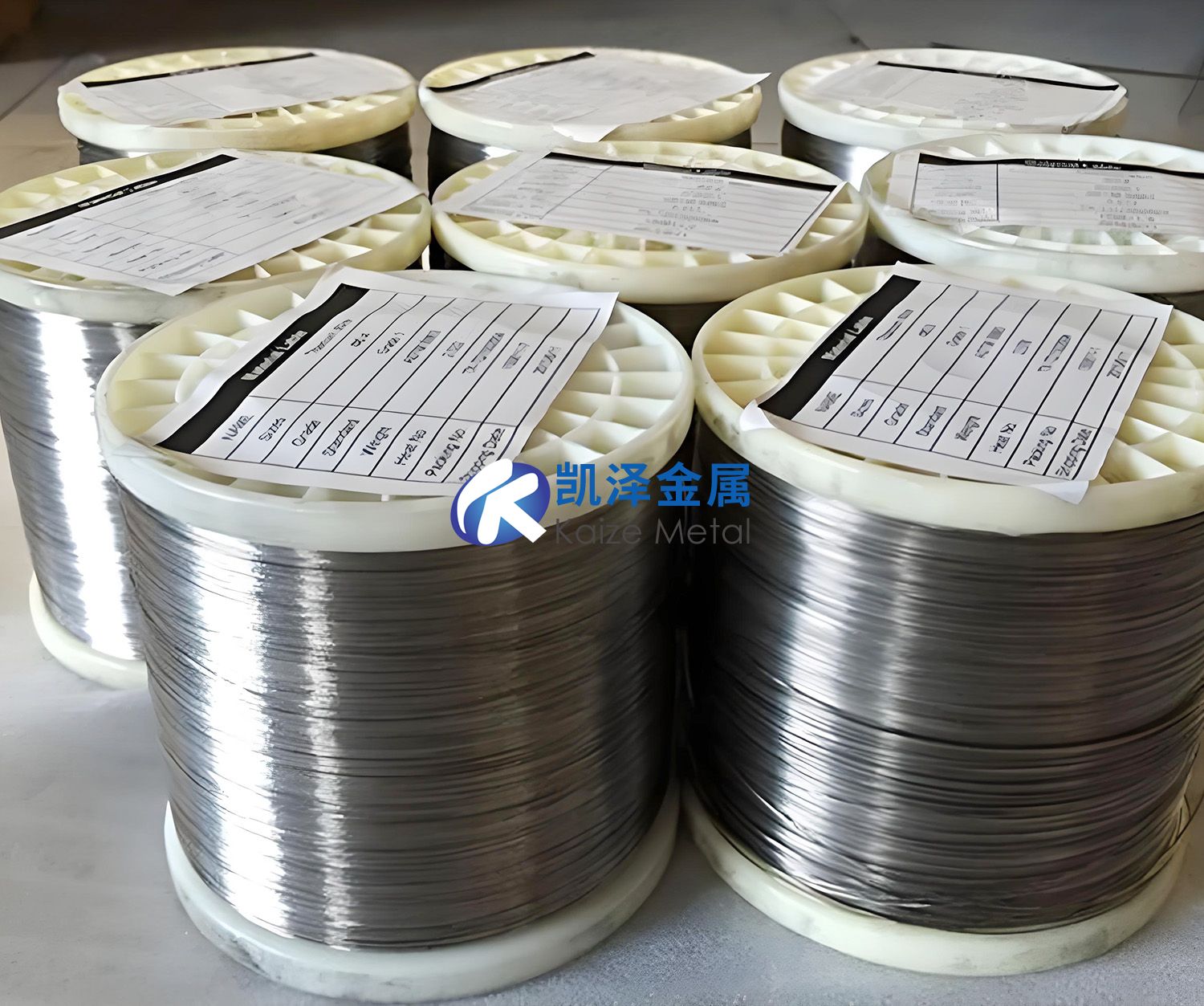
7. 國內(nèi)外產(chǎn)業(yè)化對比
維度 | 中國(2023) | 國際先進(jìn)水平 | 差距分析 |
粉末產(chǎn)能 | 800噸/年(主要<53μm) | 2500噸/年(美國AP&C) | 細(xì)粉率低15% |
打印效率 | SLM 20cm3/h | EBM 150cm3/h(Arcam Q20+) | 能量利用率差3倍 |
認(rèn)證體系 | 3項國軍標(biāo) | 22項FAA/EASA認(rèn)證 | 適航經(jīng)驗不足 |
回收技術(shù) | 50%粉末再利用 | 85%閉環(huán)回收(德國EOS) | 氧增量控制差 |
8. 未來技術(shù)路線圖
時間節(jié)點 | 技術(shù)方向 | 目標(biāo)參數(shù) | 產(chǎn)業(yè)化前景 |
2025 | 納米鈦合金粉 | 粒徑<10μm | 微納器件打印 |
流動性<15s/50g |
2028 | 梯度功能材料 | 成分連續(xù)漸變(Ti-6Al-4V→Ti-Cu) | 仿生結(jié)構(gòu)制造 |
2030 | 太空原位打印 | 月壤鈦鐵礦直接制粉 | 地外基地建設(shè) |
2035 | 智能響應(yīng)材料 | 形狀記憶鈦合金(應(yīng)變恢復(fù)率>95%) | 自適應(yīng)結(jié)構(gòu)體 |
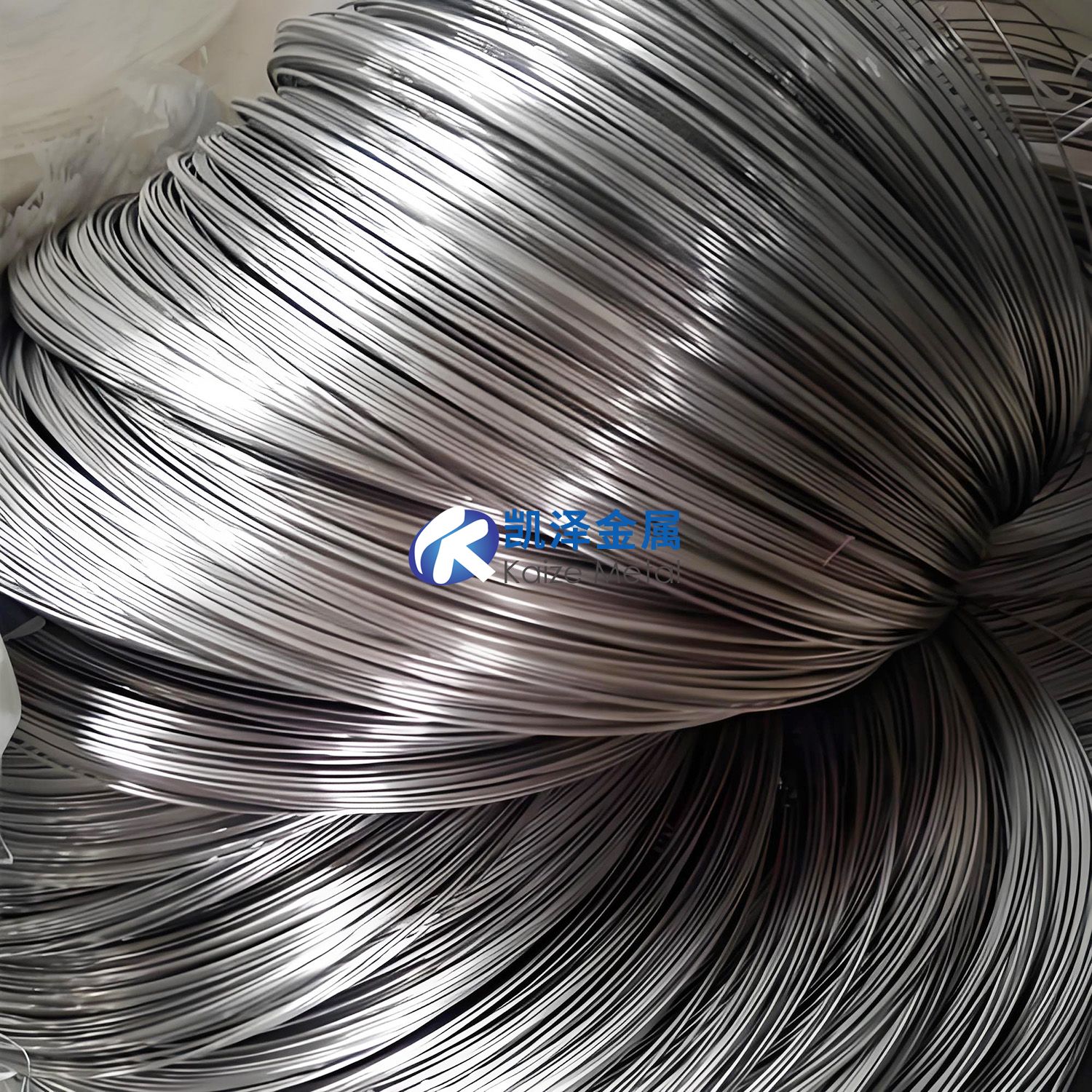
3D打印鈦合金耗材正向超細(xì)粉體化、功能梯度化、智能響應(yīng)化演進(jìn),建議優(yōu)先布局氫能/核聚變領(lǐng)域?qū)S煤辖痖_發(fā),攻克粉末低成本制備與缺陷智能檢測技術(shù),同時構(gòu)建數(shù)字孿生工藝庫實現(xiàn)know-how沉淀。短期內(nèi)可重點突破醫(yī)療植入物市場(CAGR>30%),長期需向太空制造等戰(zhàn)略領(lǐng)域延伸。
相關(guān)鏈接