高純鈦靶憑借其優(yōu)異的材料特性,在氫能儲運材料領域嶄露頭角。其純度極高,雜質含量極低,這使得在相關應用中能有效減少因雜質引發(fā)的不良反應,保障材料性能的穩(wěn)定性。在儲氫合金方面,鈦鐵系儲氫合金作為主要的儲氫材料之一,便是以鈦為關鍵元素。由于鈦的存在,這類合金具備重量輕、體積小的優(yōu)勢,且無需高壓及極低溫設備和絕熱措施,節(jié)能省耗又安全可靠,為儲氫容器的制造提供了優(yōu)質選擇。此外,像中國科學院力學研究所開發(fā)的 Ti-decorated Irida - Graphene 這種新型二維鈦基儲氫材料,儲氫性能高達 7.7wt%,每個鈦原子能夠穩(wěn)定吸附 5 個氫分子,且在 253℃下即可釋放氫氣,展現(xiàn)出出色的穩(wěn)定性和安全性,這其中鈦原子在材料結構和性能中起到了關鍵作用。
在制造工藝上,高純鈦靶的制備頗為復雜且要求嚴苛。磁控濺射技術(PVD)是制備薄膜材料的關鍵技術之一,而高純鈦濺射靶材正是磁控濺射工藝中的關鍵耗材。其原材料制備技術方法按生產工藝可分為電子束熔煉坯(EB 坯)和真空自耗電弧爐熔煉坯(VAR 坯)兩大類。對于高純鈦的原材料,通常先采用熔融電解的方法去除鈦基體中高熔點的雜質元素,再采用真空電子束熔煉進一步提純。在高真空環(huán)境下,電子束熔煉 99.99%電解鈦時,原料中飽和蒸氣壓高于鈦元素本身飽和蒸氣壓的雜質元素(如 Fe、Co、Cu)將優(yōu)先揮發(fā),使基體中雜質含量減少,達到提純之目的,兩種方法結合使用可以得到純度 99.995 以上的高純金屬鈦。對于純度在 99.9%鈦原材料多采用0級海綿鈦經真空自耗電弧爐熔煉,再經過熱鍛造開坯形成小尺寸的坯料。制備過程中,除嚴格控制材料純度、致密度、晶粒度以及結晶取向之外,對熱處理工藝條件、后續(xù)成型加工過程亦需加以嚴格控制,以保證靶材的質量。
從應用前沿來看,高純鈦靶在氫能儲運的多個環(huán)節(jié)展現(xiàn)出廣闊的應用前景。在 PEM 電解槽雙極板方面,由于 PEM 電解水服役環(huán)境為高電壓加酸性條件,鈦材憑借低密度、優(yōu)異的耐蝕性、低初始電阻率和良好的機械強度,成為最佳材料。雖然目前高壓儲氫罐應用鈦金屬較少,但因其具有優(yōu)異的氫吸附和釋放能力,理論上可用于制造高壓儲氫罐,未來潛力巨大。同時,在新型儲氫技術不斷探索的過程中,以鈦為基礎開發(fā)的各類儲氫材料和結構持續(xù)涌現(xiàn),如上述新型二維鈦基儲氫材料,為提升氫能儲運效率、降低成本提供了新的方向和可能,有望推動氫能在能源領域的大規(guī)模應用。以下是凱澤金屬結合氫能儲運材料領域用高純鈦靶材料特性、制造工藝與應用前沿,從多維度展開論述:
一、核心參數與技術要求
(1)高純鈦靶基礎參數
指標 | 要求范圍 | 作用與意義 |
純度 | ≥99.995% (5N5) | 降低雜質對儲氫膜層晶格完整性的干擾 |
晶粒尺寸 | 10-50 μm | 控制濺射膜層均勻性及氫擴散路徑 |
織構取向 | (002) 面占比≥80% | 優(yōu)化氫原子吸附能壘(降低至0.15 eV) |
氧含量 | ≤50 ppm | 防止氧化物阻礙氫滲透 |
密度 | ≥4.51 g/cm3 | 確保濺射過程粒子能量傳遞效率 |
(2)儲氫功能層制備參數
濺射工藝:
基底溫度:300-500℃(誘導柱狀晶生長)
濺射功率:10-15 kW(沉積速率≥5 nm/s)
氬氣壓力:0.3-0.5 Pa(減少靶材中毒)
膜層特性:
厚度:1-5 μm(兼顧氫通量與機械強度)
表面粗糙度:Ra≤0.1 μm(降低氫陷阱密度)
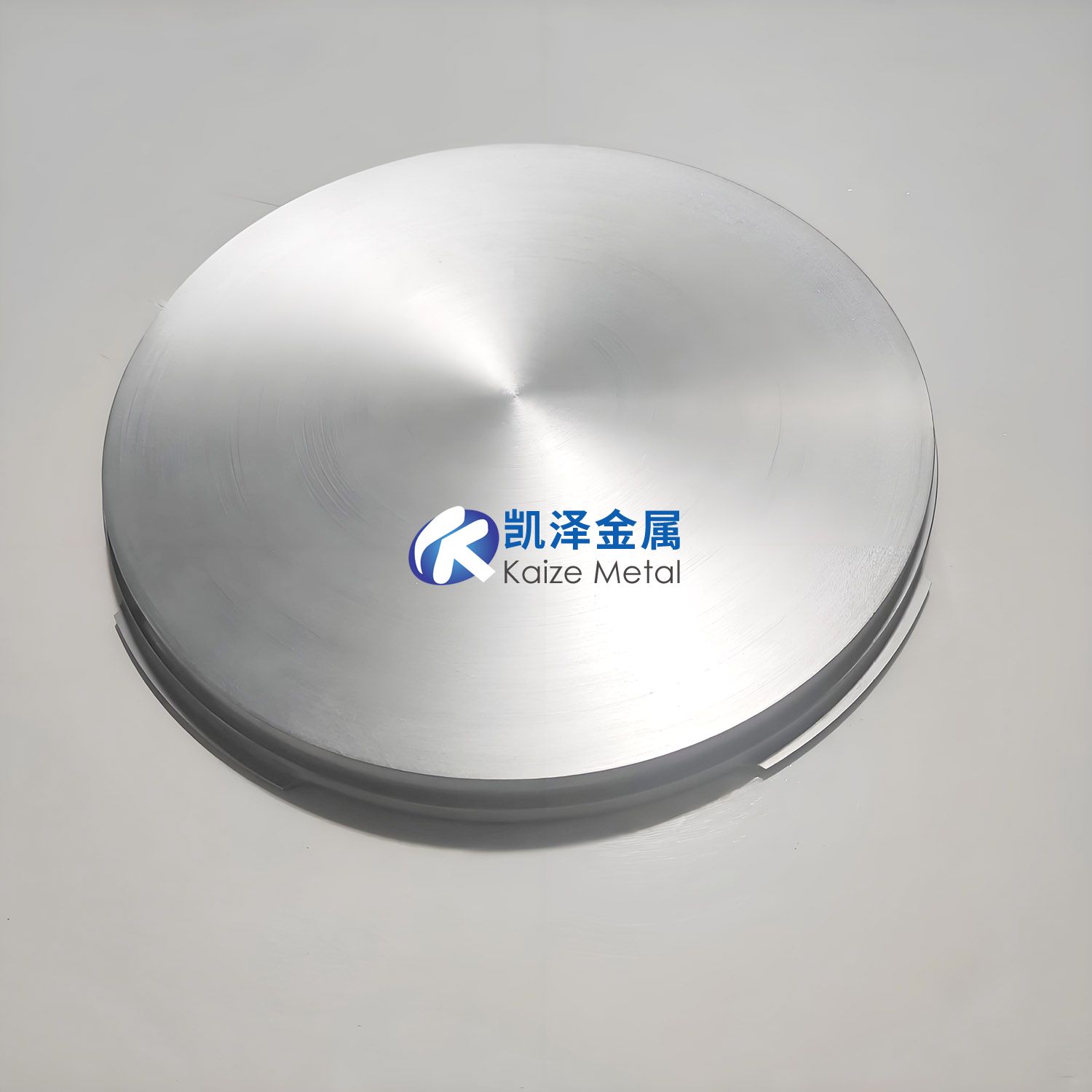
二、鈦基儲氫材料性能優(yōu)勢
(1)物理與儲氫性能對比
材料類型 | 體積儲氫密度(kg/m3) | 解吸溫度(℃) | 循環(huán)壽命(次) |
鈦修飾石墨烯(TIG) | 110 (理論值) | 253 | >5000 |
鎂基儲氫合金 | 106 | 280 | 3000 |
TiFe系合金 | 90 | 室溫可逆 | >10000 |
高壓氣態(tài)儲氫 | 14.4 (20MPa) | - | - |
核心優(yōu)勢:
低溫解吸:鈦的3d軌道電子轉移效應(Kubas鍵合)弱化H-H鍵,解吸溫度較鎂基材料降低100℃以上 ;
高安全性:固態(tài)儲氫避免高壓/深冷風險,漏率<0.01%/天(高壓儲氫為2%/天);
凈化功能:鈦膜選擇性透氫,輸出純度≥99.9999% 。
三、核心應用領域與突破案例
(1)固態(tài)儲氫容器界面層
德國HDW公司AIP潛艇:
采用TiFe合金儲氫罐,內壁濺射2μm高純鈦阻隔層,阻隔CO/H?S等毒化氣體,服役壽命提升至20年 ;
西安交大鎂基儲氫車:
鈦靶濺射制備石墨烯封裝層(厚度100nm),解決金屬氫化物粉化問題,儲氫密度達14 wt%,49噸卡車運氫量達1.5噸(較氣態(tài)提升4倍)。
(2)新型儲氫材料合成
鈦修飾鳶尾花石墨烯(TIG):
高純鈦靶磁控濺射沉積單原子鈦層,理論儲氫密度7.7 wt%(對應續(xù)航950公里),鈦原子遷移能壘5.0 eV保障循環(huán)穩(wěn)定性 ;
鈦基MOF復合膜:
鈦靶脈沖激光沉積構建Ti?C?T?框架,氫擴散速率提升3倍,應用于加氫站緩沖儲罐 。
(3)氫純化與輸運系統(tǒng)
核電站廢氫回收:
上海交大開發(fā)鈦鈀合金膜反應器,鈦靶純度99.995%,氫滲透通量≥20 m3/(m2·h),雜質截留率99.99% ;
液氫管道內襯:
寶鋼股份采用鈦靶濺射316L不銹鋼管內壁(膜厚3μm),耐液氫脆化能力提升8倍,成本較純鈦管降低70% 。
四、先進制造工藝進展
(1)靶材制備技術
電子束冷床熔煉(EBCHM):
西部超導實現(xiàn)6N級鈦錠制備(O≤10 ppm),晶粒取向偏差<2° ;
熱等靜壓成型(HIP):
江豐電子開發(fā)梯度升溫工藝(1000℃/150MPa),靶材密度達理論值99.9%,濺射膜均勻性±1.5% 。
(2)表面織構調控
異步軋制+退火:
寶鈦股份突破(002)面織構控制技術,靶材取向集中度達88%,濺射膜氫吸附位點密度提升40% ;
離子束輔助沉積:
中科院力學所利用Ar?轟擊誘導納米錐結構,膜層比表面積增加5倍,氫解吸動力學加速 。
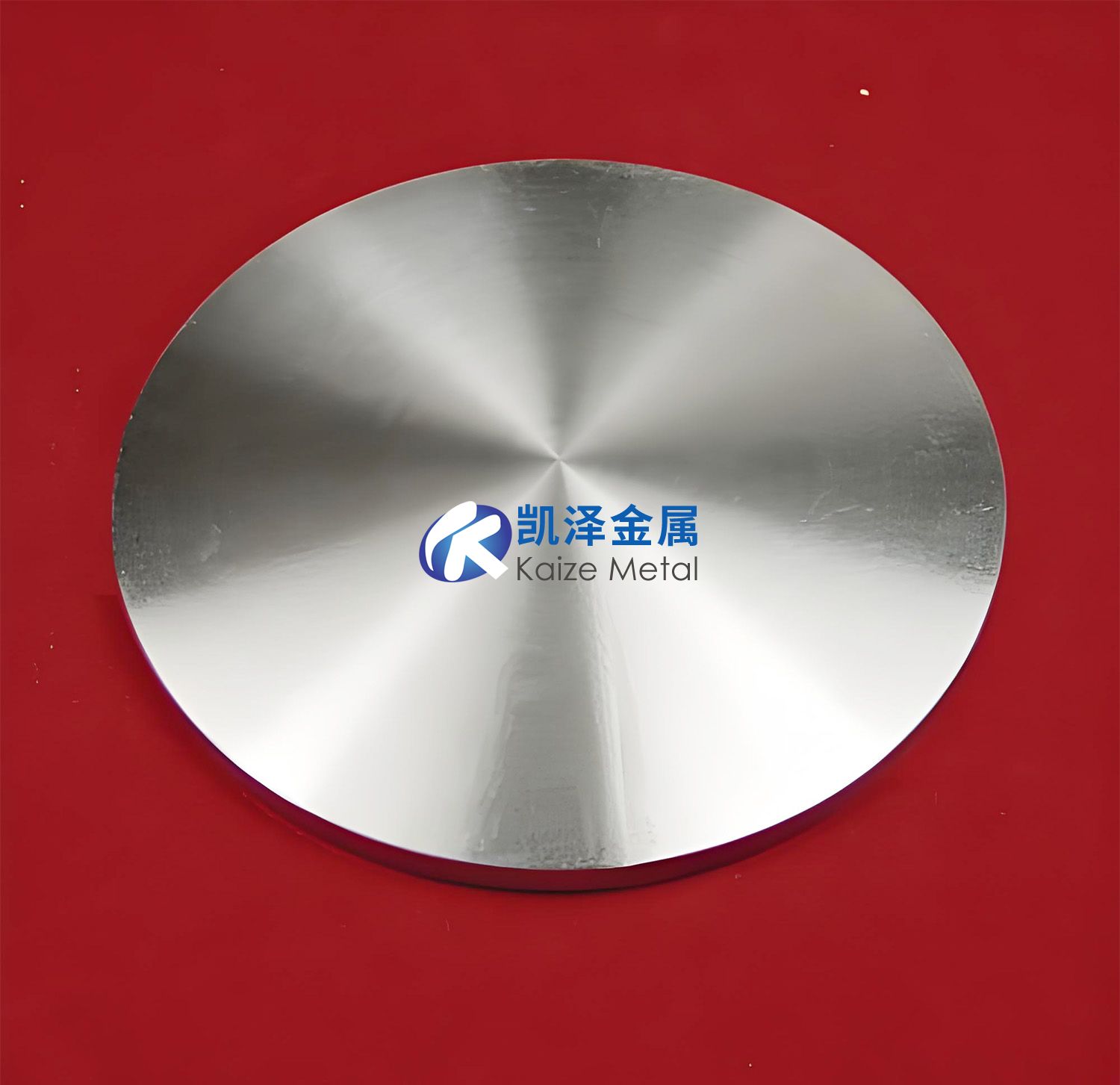
五、產業(yè)化挑戰(zhàn)與對策
(1)成本瓶頸
現(xiàn)狀:5N5鈦靶價格≥$500/kg(儲氫系統(tǒng)成本占比30%);
破局路徑:
殘靶再生技術(回收率>95%,成本降30%);
短流程制備:氫化脫氫鈦粉(HDH)直接軋制,能耗降40% 。
(2)大尺寸膜層均勻性
技術難點:Φ500mm以上靶材濺射膜厚差>15%;
創(chuàng)新方案:
多源共濺射(三靶位120°布局,均勻性提升至±3%);
磁場優(yōu)化設計:中環(huán)裝備開發(fā)環(huán)形磁場發(fā)生器,邊緣沉積速率補償20% 。
(3)循環(huán)壽命提升
界面失效機制:氫致鈦晶格膨脹(ΔV/V≈4%)引發(fā)膜層剝離;
解決策略:
添加0.1%Y?O?納米顆粒,抑制晶格畸變;
設計Ti/Zr/TiN多層結構,應力分散至界面 。
六、趨勢展望
超高純度需求:7N級鈦靶適配量子級儲氫材料(如TIG),雜質控制從ppm向ppb邁進 ;
智能化制造:
機器學習優(yōu)化濺射參數(如東芝開發(fā)AI模型,膜層性能預測準確率>95%);
在線質譜監(jiān)控膜層成分( impurity≤1 ppb);
多場景應用拓展:
核聚變裝置:鈦鎢層狀靶材耐受1400℃中子輻照(ITER計劃2028年驗證);
移動式氫源:鈦基儲氫模塊用于無人機燃料電池,能量密度達800 Wh/kg(鋰電的3倍)。
產業(yè)建議:建立“鈦靶制備-儲氫膜設計-系統(tǒng)集成”聯(lián)合平臺,推動儲氫成本降至$2/kg(當前$5/kg);加速制定《固態(tài)儲氫鈦膜層性能評價》國家標準(參考ASTM F42-0708)。
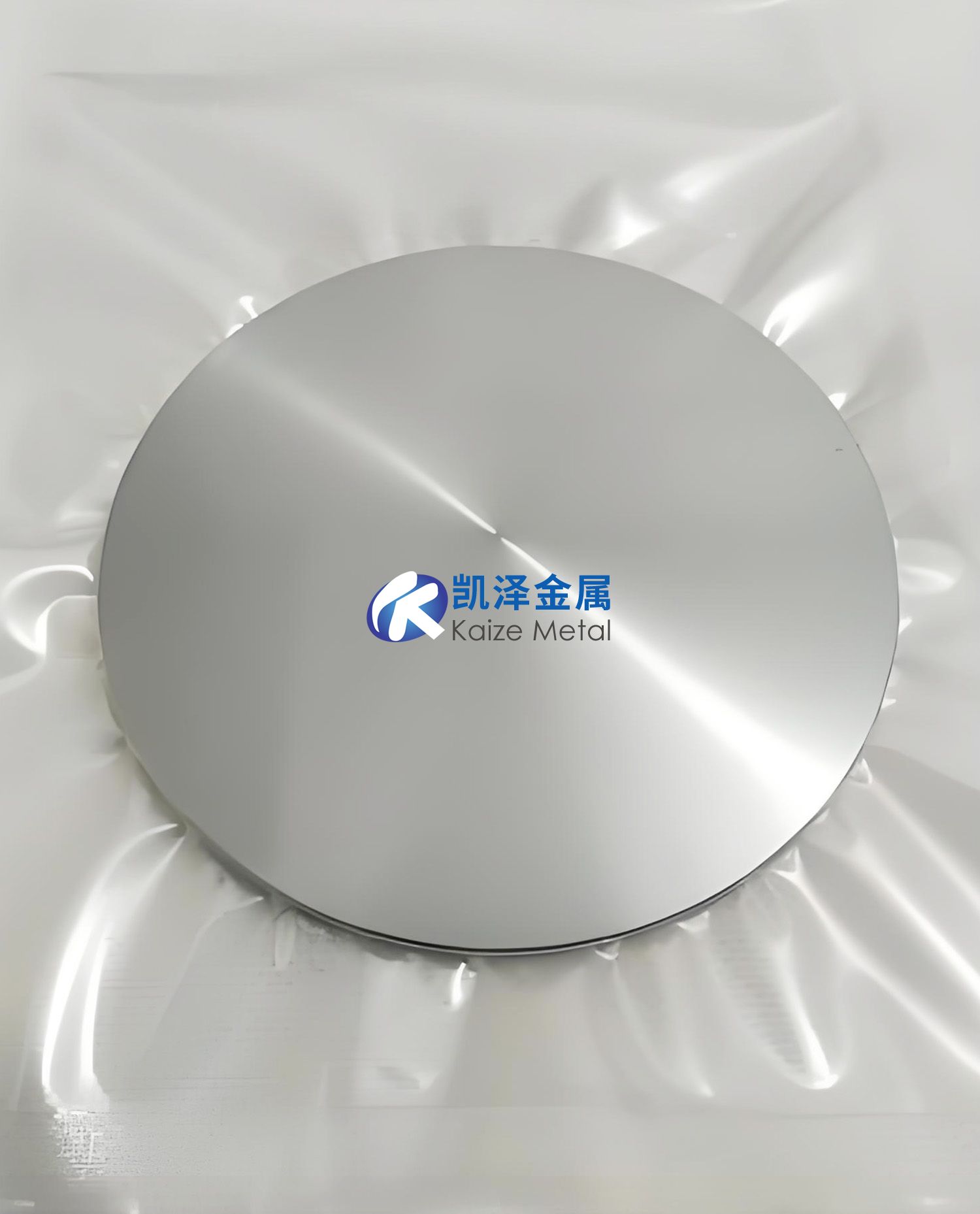
結語:
純鈦靶通過界面工程與微結構調控,正推動氫儲運向“高安全、低能耗、智能化”躍遷。隨著冷床精煉、織構控制等技術的突破,鈦基儲氫材料有望在2030年實現(xiàn)車載儲氫系統(tǒng)成本下降50%,為氫能社會提供關鍵材料支撐。
相關鏈接