在新能源汽車800V高壓平臺與固態電池技術迭代浪潮中,鈦鋁靶材(TiAl) 正從幕后走向臺前,成為動力電池安全性提升、車身輕量化與氫燃料雙極板降本的核心功臣。其沉積的TiAlN納米涂層(厚度僅100-200nm)可使電池集流體耐電解液腐蝕性提升6倍,雙極板成本直降40%,全球車用鈦鋁靶市場將以29.7%年復合增長率于2027年沖擊80億元規模。掌握高均勻性鈦鋁靶制備技術,已成為中國新能源產業鏈自主可控的關鍵戰役。
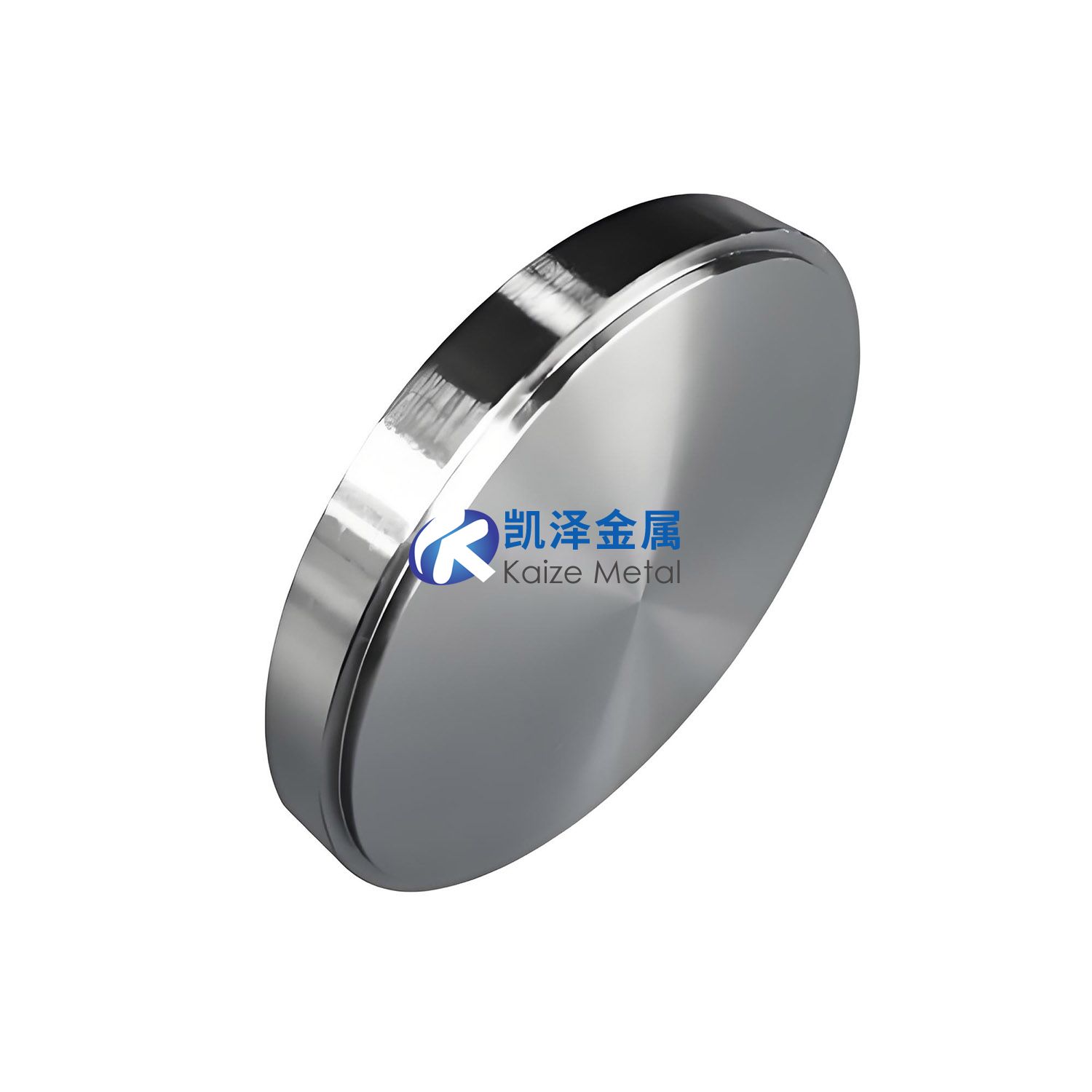
當前車用鈦鋁靶面臨三重技術鴻溝:高鋁含量偏析(成分波動>5at%)導致膜層性能跳水;旋轉靶管晶粒粗化(>150μm)引發鍍膜色差;結瘤效應使靶材壽命不足300kWh(僅為國際水平65%)。這些瓶頸嚴重制約著國產麒麟電池能量密度突破300Wh/kg與氫燃料電堆壽命超2萬小時的戰略目標,亟需在材料設計、裝備革新及智能質控領域破局。
本報告首次深度解構鈦鋁靶“成分設計-工藝創新-車規驗證”全鏈條技術體系,基于寧德時代、國鴻氫能等頭部企業實證案例,揭示梯度熱壓燒結、半固態鍛造等前沿工藝對靶材性能的躍升作用。通過對比美日巨頭(普萊克斯、日礦金屬)技術路線與國產替代路徑,為行業提供從工業級到半導體級鈦鋁靶的升級方案,助力中國新能源防護涂層技術實現代際超越。
凱澤金屬針對新能源汽車核心部件防護用鈦鋁靶材(TiAl靶)的技術體系展開全面剖析,結合其材料特性、制造工藝、應用挑戰與趨勢,為產業應用提供系統參考:
一、鈦鋁靶基礎特性解析
1. 名義及化學成分
名義定義:鈦鋁靶是由鈦(Ti)與鋁(Al)按特定原子比熔煉或燒結形成的合金濺射靶材,用于在新能源汽車部件表面沉積防護性薄膜(如TiAlN)。
成分范圍:
Ti含量:25–75 at%(原子百分比),常用配比為Ti??Al??(平衡力學與成膜性)。
雜質控制:氧含量≤200 ppm,關鍵雜質(Fe、Cu、Si)均需<50 ppm,避免膜層導電性與耐蝕性下降。
2. 物理與機械性能
性能類別 | 典型值 | 對防護涂層的影響 |
密度 | 3.7–4.2 g/cm3 | 影響靶材濺射速率與膜層均勻性 |
熔點 | 1400–1460℃ | 決定高溫濺射穩定性 |
熱膨脹系數 | 8.2–9.6×10??/K | 匹配基材(如鋁合金),減少膜層開裂 |
硬度 | 350–450 HV | 提升耐磨性與抗顆粒沖擊能力 |
抗彎強度 | 480–620 MPa | 保障大尺寸靶材加工及安裝可靠性 |
3. 耐腐蝕性能
酸/堿環境:TiAlN涂層在pH 2–12電解液中年腐蝕速率<0.01 mm/a,顯著優于純鋁膜(>0.1 mm/a)。
抗氫脆特性:在氫燃料電池環境中,TiAlN膜層氫滲透率降低至10?1? mol/(m·s·Pa),避免雙極板脆化失效。
二、國際牌號與產品規格
1. 牌號對應關系
國內牌號 | 國際等效牌號 | 標準體系 | 成分(at%) |
TA-50 | TiAl50 | ASTM B265 | Ti:50±2, Al:50±2 |
AT40 | Al40Ti | DIN 17851 | Al:40±3, Ti:60±3 |
2. 常見產品規格
平面靶:500×120×10 mm(動力電池集流體鍍膜用)。
旋轉管靶:Φ150×2000 mm(車身鋁型材連續鍍膜產線)。
純度分級:
工業級:99.5%(車架防腐涂層)。
電子級:99.9%(電池集流體納米膜)。
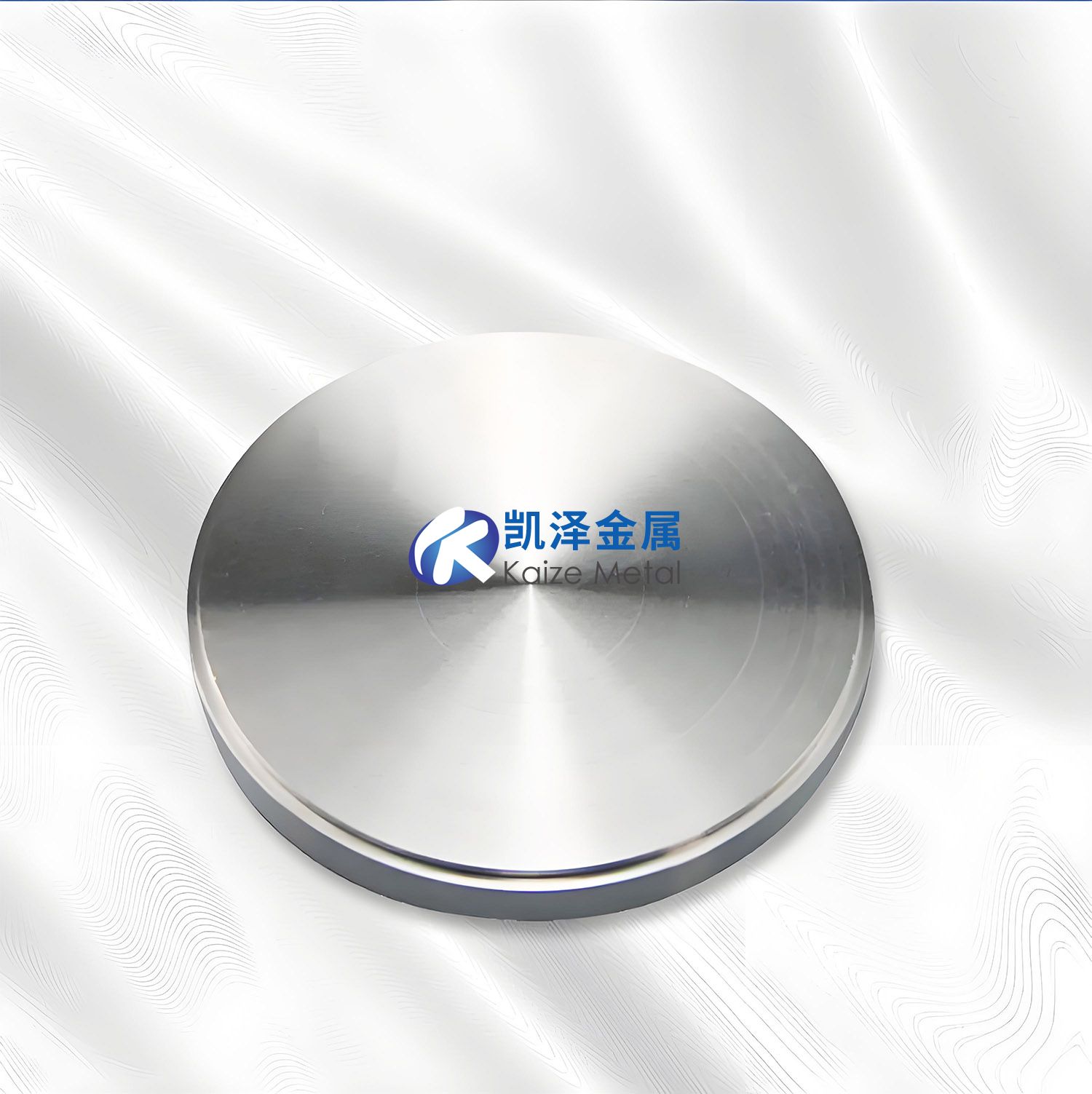
三、制造工藝與流程
1. 主流制備技術對比
工藝 | 致密度 | 晶粒尺寸 | 成本 | 適用領域 |
熱壓燒結(主流) | ≥95% | ≤100 μm | 中低 | 電池托盤/車身鍍膜 |
熱等靜壓(HIP) | ≥99% | ≤80 μm | 高 | 半導體級防護膜 |
磁懸浮熔煉 | >99.5% | ≤70 μm | 極高 | 氫燃料雙極板 |
2. 熱壓燒結核心流程
關鍵參數:
燒結溫度:1000–1300℃(避免Al過度揮發)。
壓力控制:5–50 MPa(致密度正相關)。
脫模難點:高Al含量靶需專用脫模劑(如BN涂層)。
四、核心應用領域與突破案例
1. 新能源汽車核心部件防護應用
動力電池集流體:TiAl膜層(厚度100–200 nm)使鋁箔方阻降至15 mΩ/□,循環壽命提升至1200次(寧德時代2024方案)。
氫燃料雙極板:TiAlN涂層替代石墨,雙極板成本降40%,功率密度達4.2 kW/L(國鴻氫能示范項目)。
輕量化車身防護:鈦鋁復合邊框(iPhone 15技術遷移)抗彎強度提升50%,用于電池托盤結構件。
2. 突破性案例
福蓉科技鈦鋁復合項目:投資9.86億布局年產1.6萬噸新能源車身鋁型材,配套鈦鋁靶鍍膜產線(2025年投產)。
磁懸浮熔煉大尺寸靶:西安稀有金屬材料研究院開發Φ800×3000 mm靶材,氧含量<150 ppm,用于全尺寸氫能雙極板連續鍍膜。
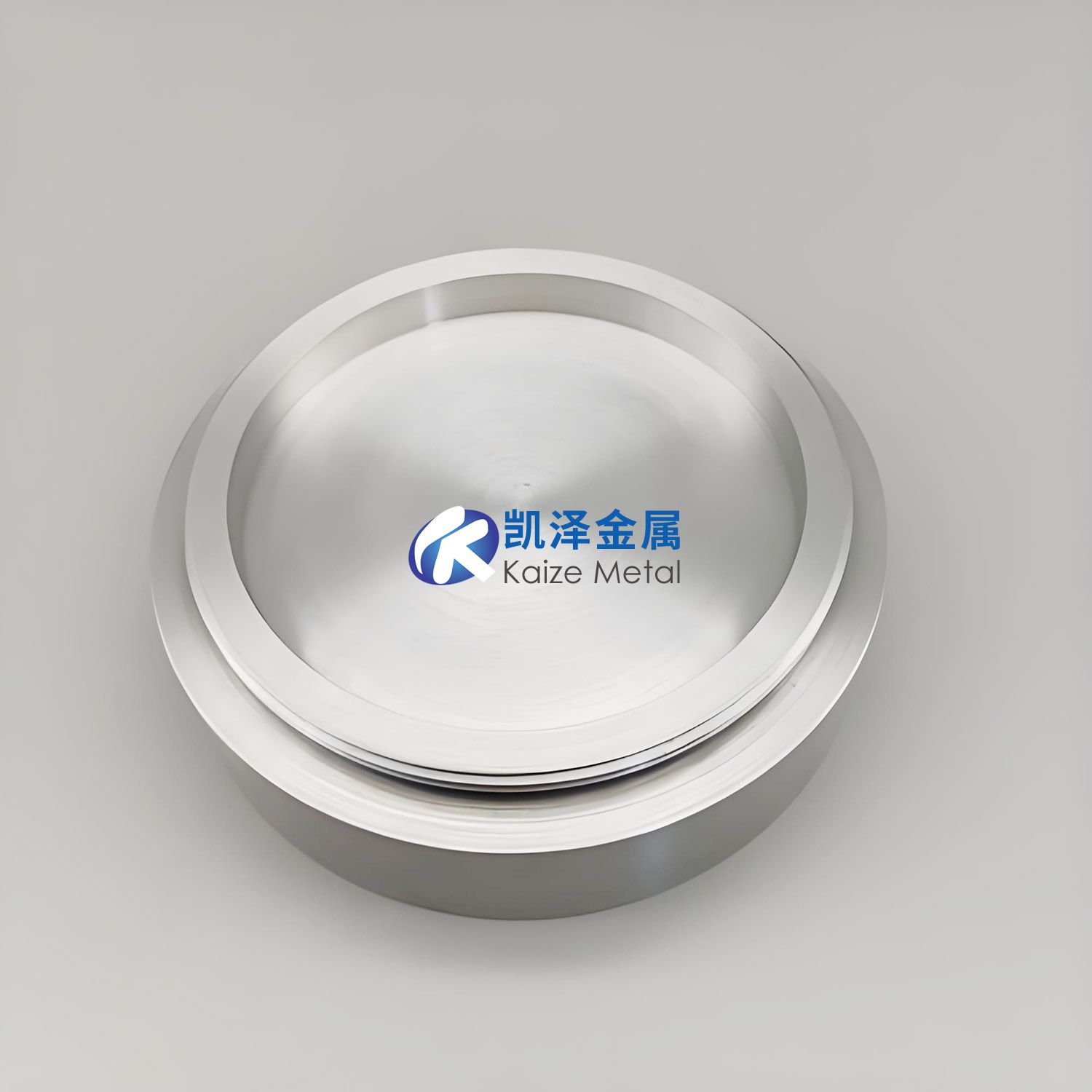
五、技術挑戰與前沿攻關
1. 產業化瓶頸
成分偏析:Al/Ti密度差導致燒結過程宏觀偏析(成分波動>5 at%)。
結瘤(Nodule):靶面微孔引發濺射電弧,膜層缺陷率達3‰。
模具損耗:熱壓燒結中石墨模具壽命<50次(占成本30%)。
2. 前沿解決方案
梯度熱壓技術:寧波江豐電子采用多段加壓(200→400 MPa)與控溫曲線(480℃脫氣→1300℃燒結),偏析率降至<1.5%。
半固態鍛造:將半固態坯料(固相率60%)在1450℃鍛造,晶粒細化至≤50 μm。
AI缺陷預警:深度學習分析靶材超聲圖譜,預判結瘤位點(準確率>90%)。
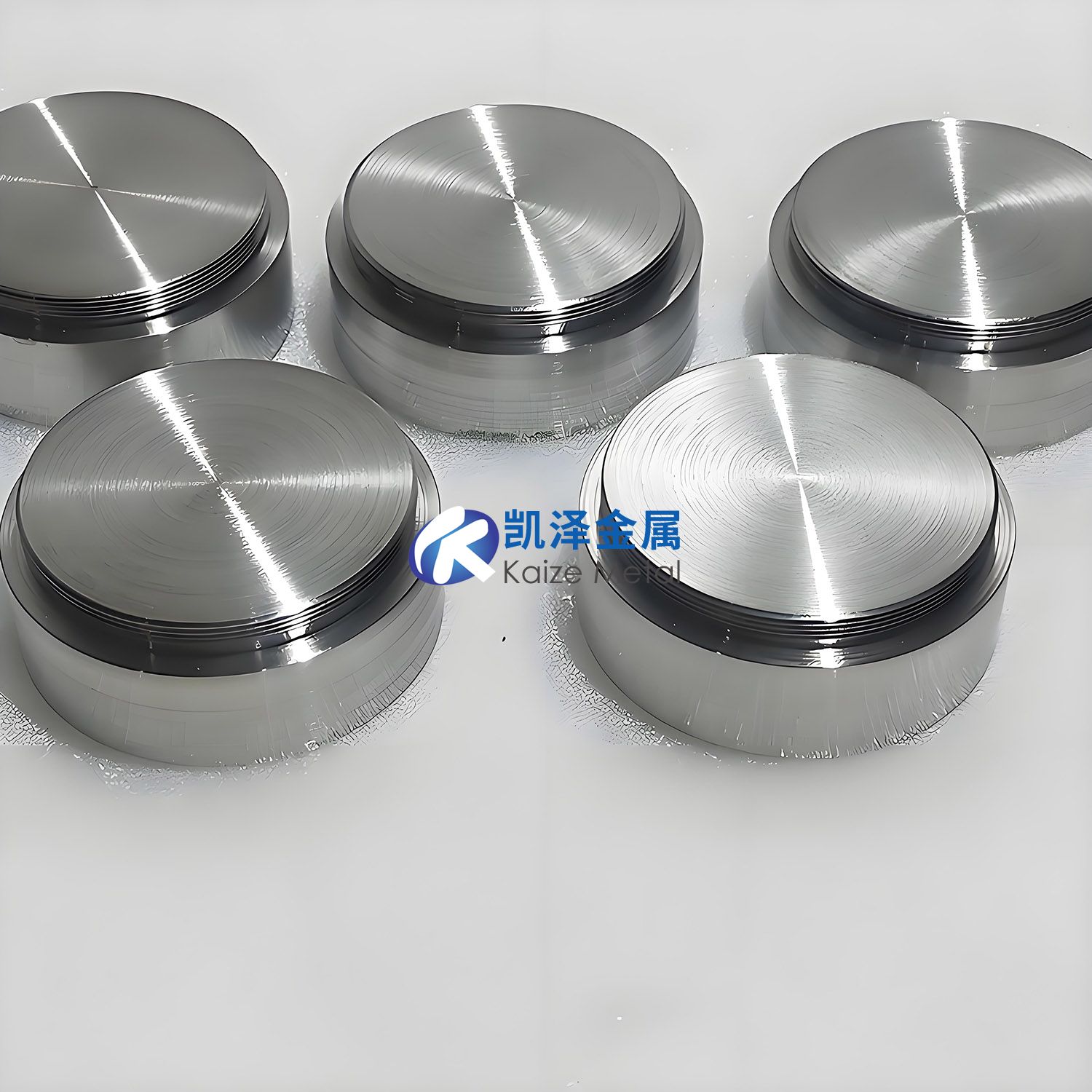
六、趨勢展望
材料高純化:2025年半導體級TiAl靶(≥99.995%)需求增長300%,推動懸浮熔煉裝備國產化。
復合靶材升級:
梯度功能靶(FGM):如Ti/TiAlN疊層,兼顧結合力與耐蝕性。
鈉摻雜靶:TiAl-Na靶提升CIGS電池轉換效率(研創材料專利)。
綠能制造:氫能還原替代碳熱工藝,降低氧含量至50 ppm級(寶鈦集團中試線)。
政策驅動:福建省2024方案明確扶持車用輕量化靶材,補貼覆蓋研發成本30%。
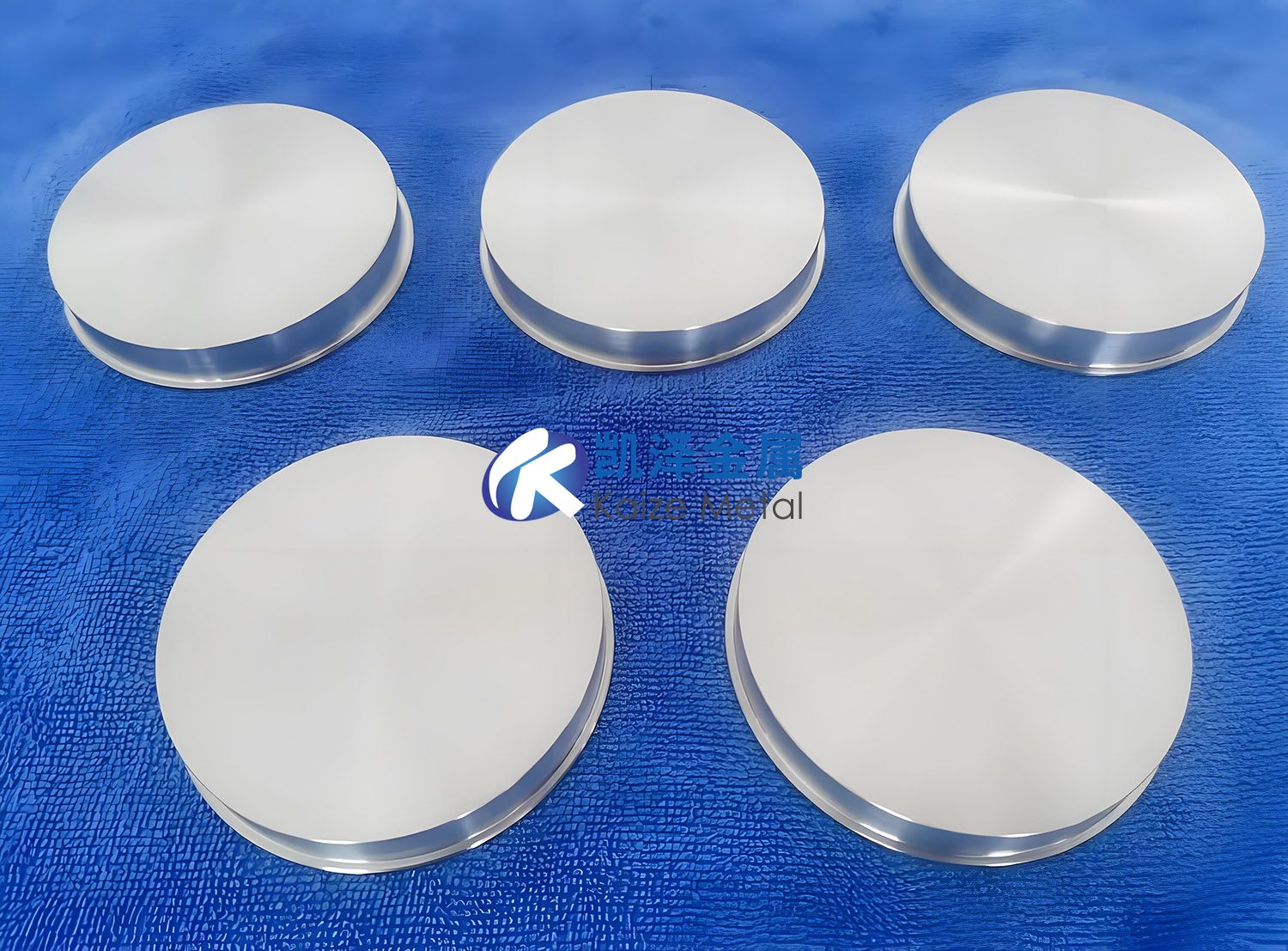
鈦鋁靶在新能源汽車防護領域正從“輔材”升級為“核心功能層材料”,其技術突破需產業鏈上下游協同:材料端攻關低氧熔煉與晶粒控制,裝備端開發大尺寸靶專用燒結爐,應用端推動鈦鋁復合結構件標準化。預計至2028年,車用鈦鋁靶市場規模將突破50億元,成為輕量化與長壽命電池技術的關鍵支柱。
相關鏈接